New benchmark for spodumene powder making! Liming Heavy Industry helps with the annual production of 20,000 tons of battery-grade lithium carbonate project
In the wave of global energy transformation, China is reshaping the lithium battery industry with the advantages of the entire industrial chain. In 2024, China's total lithium-ion battery production will reach 1170GWh, a year-on-year increase of 24%, dominating the global total production. Six of the top ten power battery companies in the world are Chinese companies, and CATL and BYD lead the global market with market shares of 37.9% and 17.2% respectively. As an irreplaceable strategic raw material for lithium battery positive electrode materials, spodumene's resource conversion efficiency and technological innovation level are becoming the key yardsticks for measuring the core competitiveness of the industry.
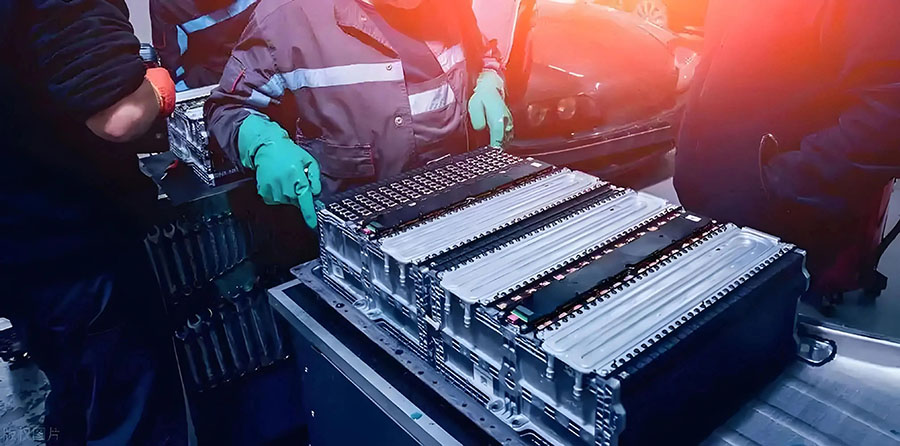
Project overview:
As the main force in the field of domestic lithium battery material manufacturing, the customer adopts the international mainstream spodumene lithium extraction process, relying on mature technical routes such as high-temperature roasting and sulfuric acid leaching, and has built a large-scale production base with an annual output of 20,000 tons of battery-grade lithium carbonate. The project achieves efficient conversion of lithium resources by importing high-grade spodumene concentrate and combining it with domestic independently optimized lithium extraction technology, and the single-line production capacity reaches the industry-leading level.
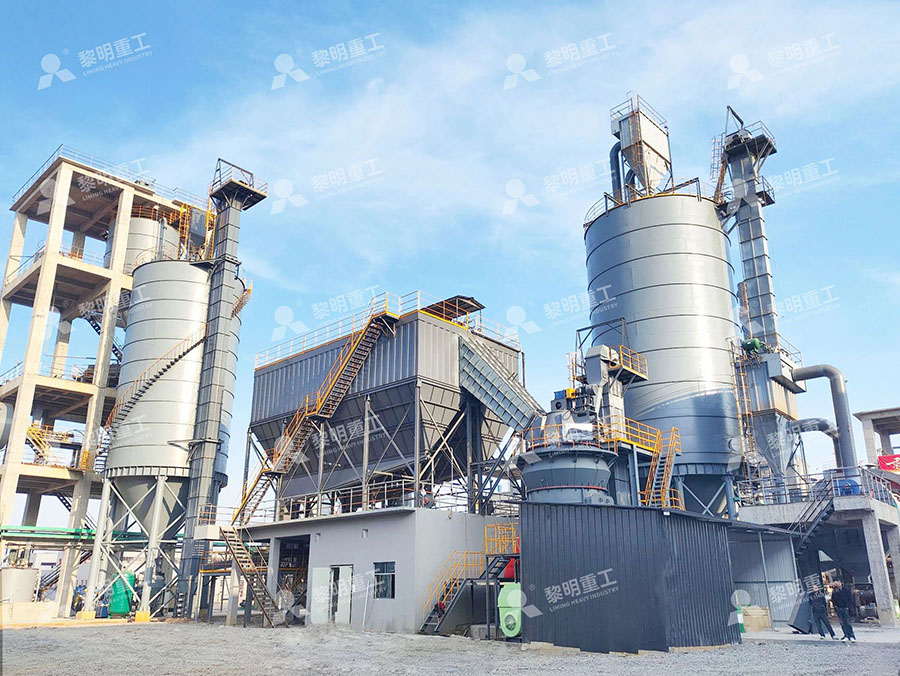
Based on the rigorous evaluation of equipment stability, process adaptability and full life cycle service capabilities, the customer finally selected Liming Heavy Industry as a strategic partner after multiple rounds of technical benchmarking. As a pioneer in global powder new material grinding equipment technology and system solutions, Liming Heavy Industry provides the project with an integrated service of "design and supply - construction and commissioning - training and after-sales", using high-quality grinding equipment technology and perfect after-sales service guarantees to ensure that the entire project meets the expected standards, high-quality delivery and smooth production!
Processing materials: roasted spodumene
Equipment used: Liming Heavy Industry LM vertical roller mill
On-site report:
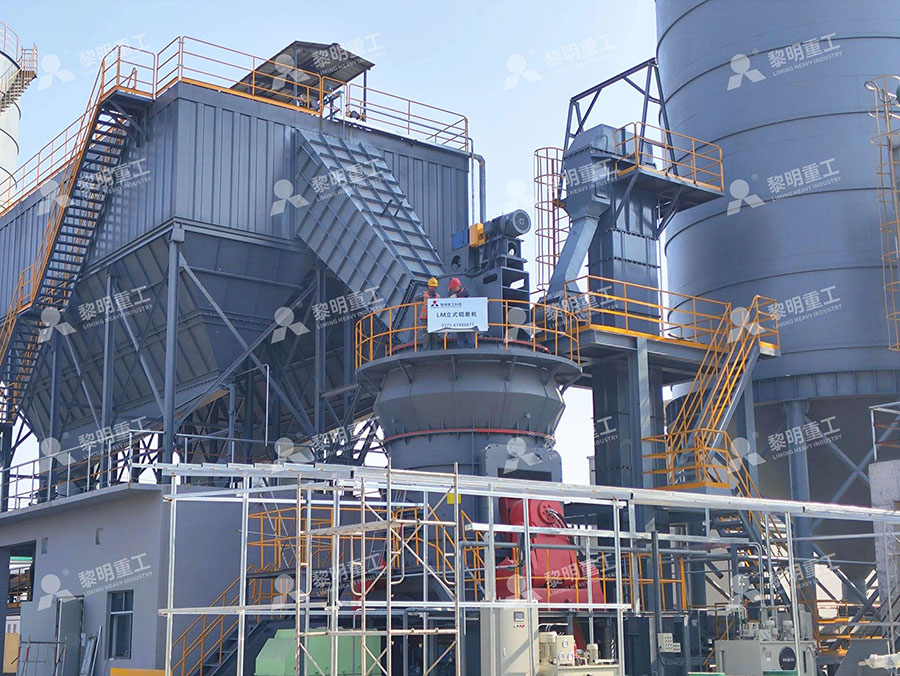
▲Liming Heavy Industry LM vertical roller mill
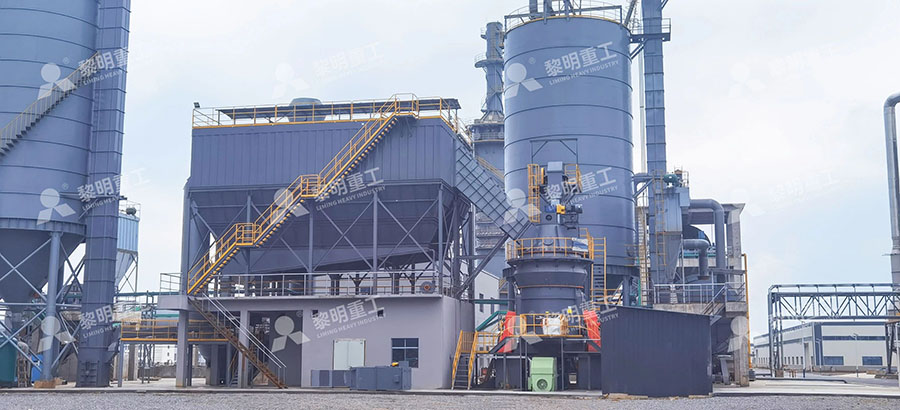
▲Intelligent production line of spodumene powder
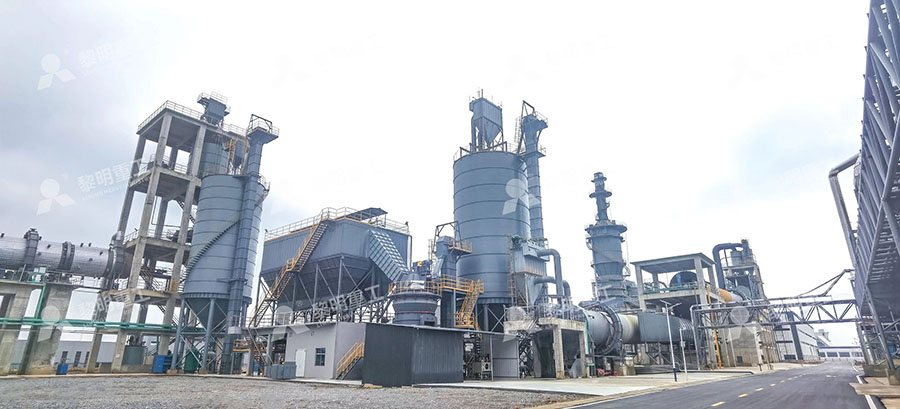
▲Lithium battery material production base
Hard-core product support:
LM series vertical roller mill is a special equipment for the preparation of key materials in the new energy industry. It is a large-scale, high-efficiency and energy-saving grinding product developed by Liming Heavy Industry with the comprehensive introduction of German Loesche and Feifan and other advantageous technologies, combined with our company's nearly 40 years of R&D and manufacturing experience. It integrates crushing, drying, grinding, grading and conveying. It has a number of independent patent technologies and intellectual property rights, and its main technical and economic indicators have reached the international advanced level.
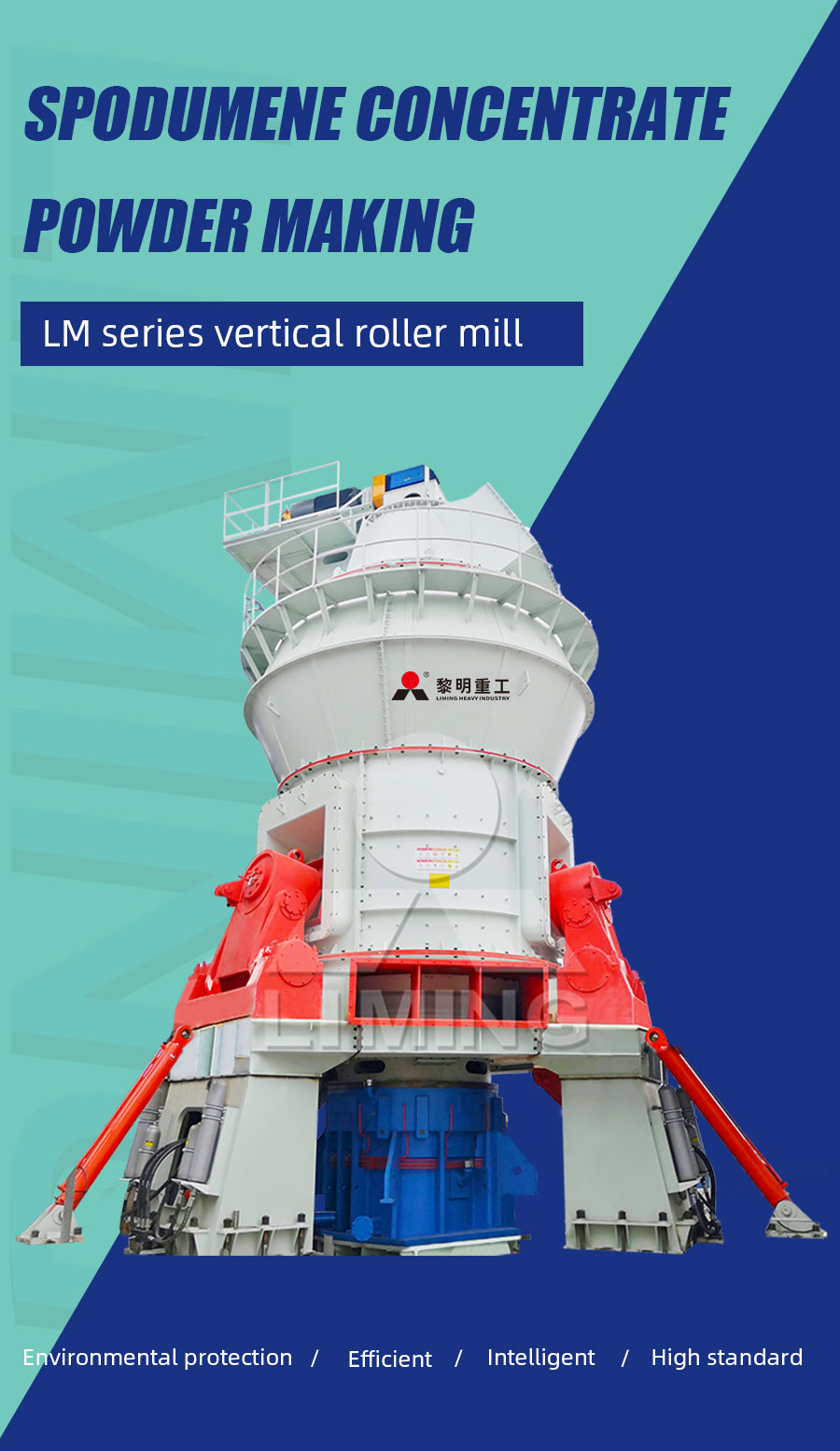
1. Leading technology and low investment cost
Integrating crushing, grinding, drying, powder selection and conveying, the layout is compact, and it can be arranged in the open air, which greatly reduces the investment cost.
2. High grinding efficiency and good product quality
Special grinding roller and grinding disc structure design, high grinding efficiency; uniform particle size distribution of finished products, and good quality of finished powder.
3. Reliable quality and stable operation
The grinding roller is equipped with a limit device to avoid direct contact between the grinding roller and the grinding disc, with low vibration; it has an automatic slag discharge function to ensure the safe operation of the equipment.
4. Large drying capacity and wide adaptability
Hot air can be used to convey materials, and materials with a moisture content of up to 15% entering the mill can be dried, and the moisture content of the materials leaving the mill is less than 1%, with a wide range of adaptability.
5. High degree of automation
The automatic control system is adopted, which can realize remote control, interlocking protection, reliable operation and simple operation.
6. Convenient maintenance and low operating cost
The grinding roller adopts forced thin oil lubrication and is equipped with a hydraulic roller turning device. During maintenance, the grinding roller can be turned out of the machine by the hydraulic device without disassembly, which is convenient and quick.
Working principle and process flow:
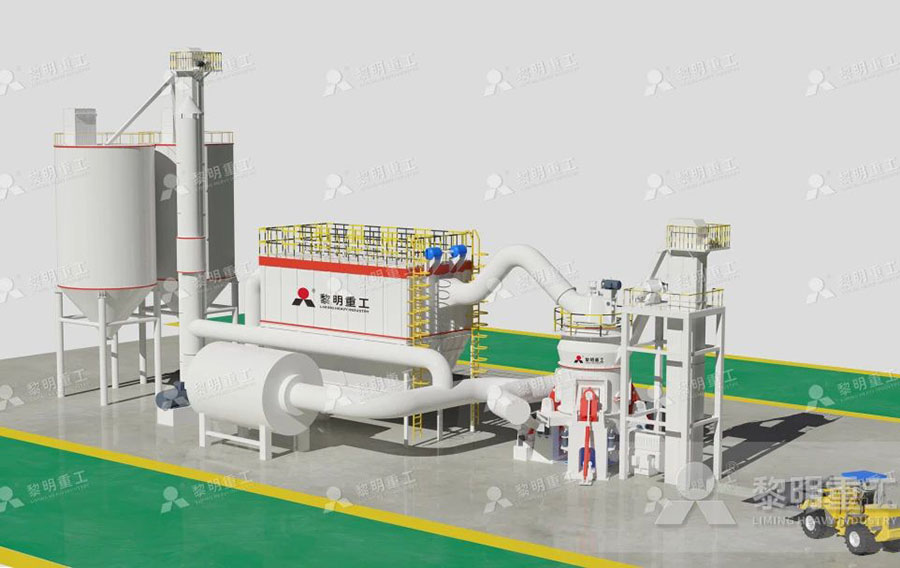
The motor drives the reducer to drive the grinding disc to rotate. The material to be ground is fed into the center of the rotating grinding disc by the air-locking feeding device. Under the action of centrifugal force, the material moves to the periphery of the grinding disc and enters the grinding roller. Under the action of the roller pressure, the material is crushed by extrusion, grinding and shearing. At the same time, hot air is ejected upward at high speed and evenly from the wind ring surrounding the grinding disc. The ground material is blown up by the high-speed airflow at the wind ring. On the one hand, the coarser material is blown back to the grinding disc for re-grinding, and on the other hand, the suspended material is dried. The fine powder is brought into the separator by the hot air for classification. The qualified fine powder is discharged from the mill along with the air flow and collected by the dust collecting equipment as the product. The unqualified coarse powder falls back to the grinding disc under the action of the separator blades and is re-grinded with the newly fed material. This cycle completes the whole grinding operation.