LM vertical roller mill helps the ceramic industry to usher in a new era of efficient and high-quality production
In terms of ceramic raw materials, shale and silica sand have gradually become the focus of attention. Shale is a widely existing sedimentary rock, and its unique geological origin gives it complex and diverse components and characteristics. Silica sand is mainly composed of silicon dioxide, and it is unique in the field of materials with its high hardness and excellent chemical stability. Liming Heavy Industry has continuously optimized the powder making technology and equipment for the ceramic field, focusing on the research of shale and silica sand powder making technology, and is committed to improving the quality and performance of ceramic raw materials, injecting strong impetus into the development of the ceramic industry.
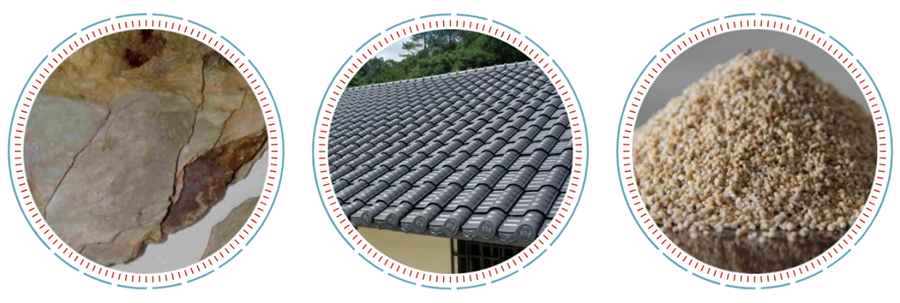
The user is a large domestic ceramic production enterprise. It focuses on the application of shale and silica sand powder in the ceramic industry, which has far-reaching significance for promoting the development of the ceramic industry and improving product quality. Liming Heavy Industry is fully responsible for planning and designing the entire production line to ensure that the layout of the production site is reasonable and compact.
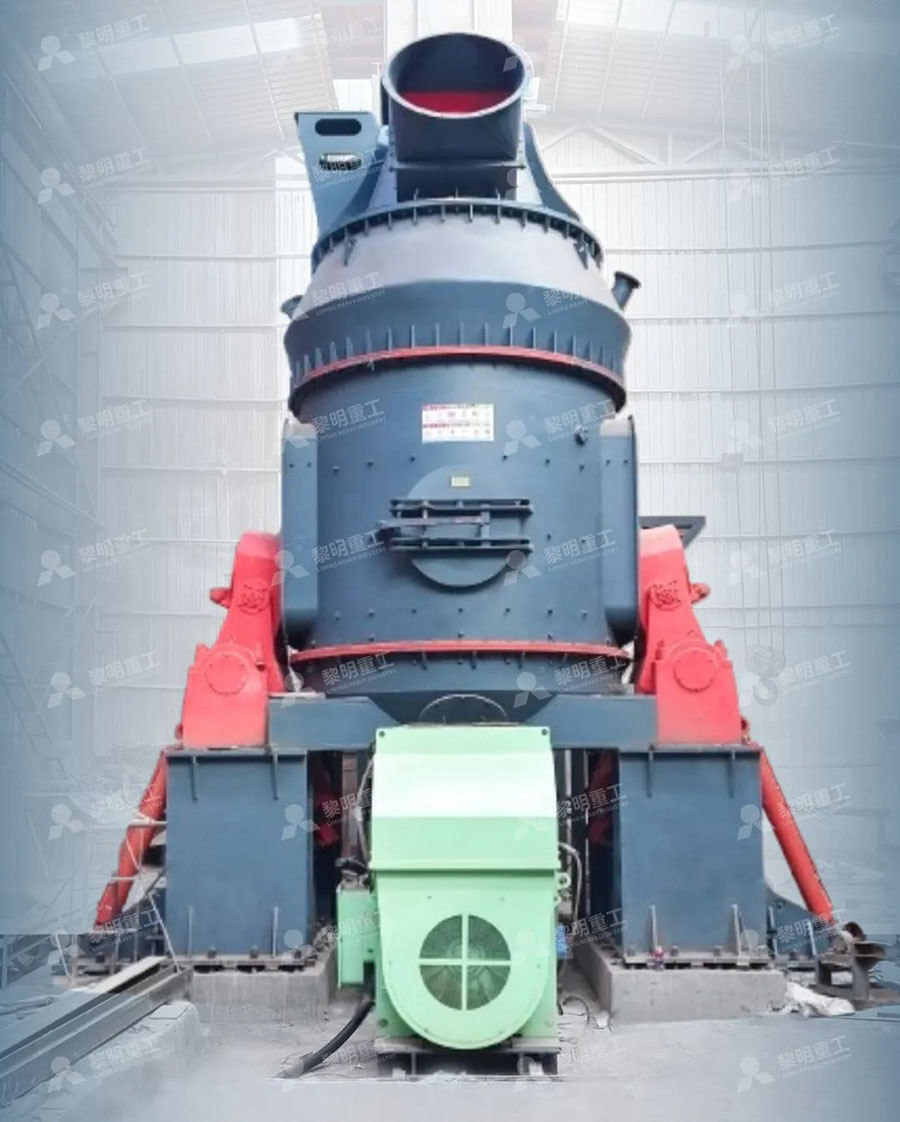
Processing materials: shale, silica sand
Finished product use: ceramics
Equipment used: LM vertical roller mill
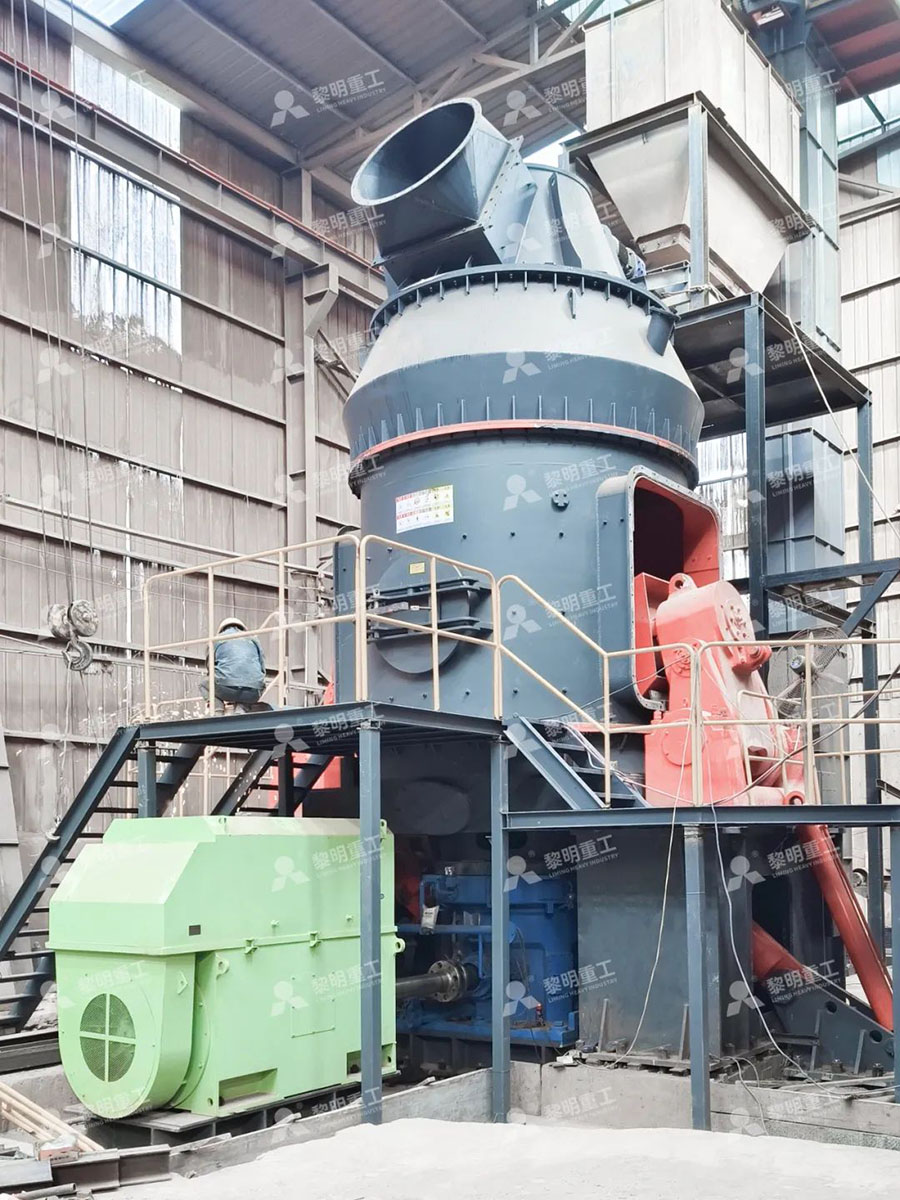
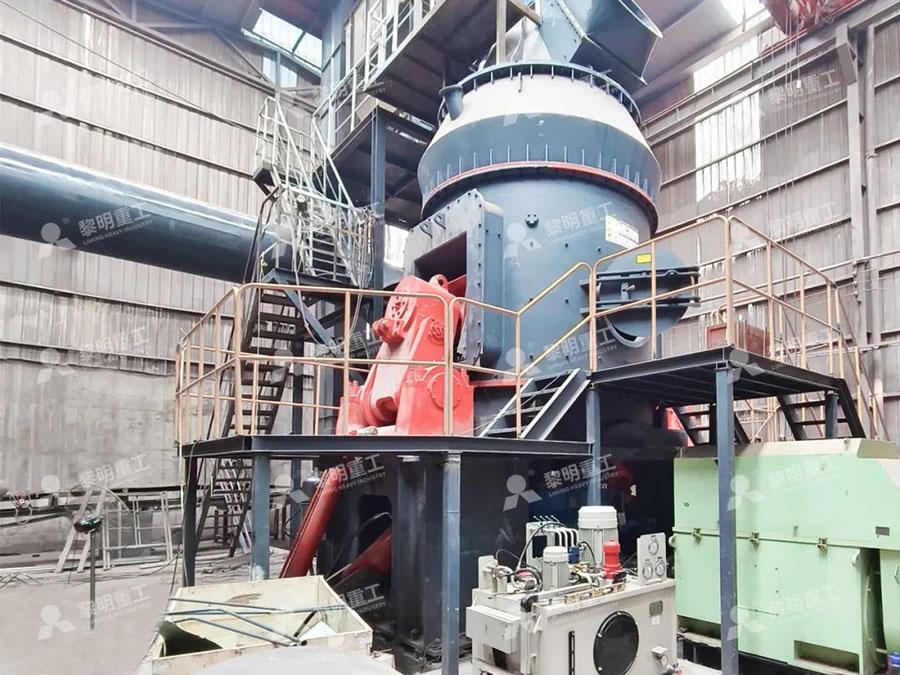
Liming Heavy Industry LM vertical roller mill integrates grinding, drying, powder selection and transportation. It meets the high standard requirements of material grinding. It can not only achieve high product purity and precise particle size control, but also save energy and reduce consumption, and has a high degree of intelligence. It can produce stably and continuously for 24 hours. Users can make diversified choices according to production, fineness, investment and other requirements.
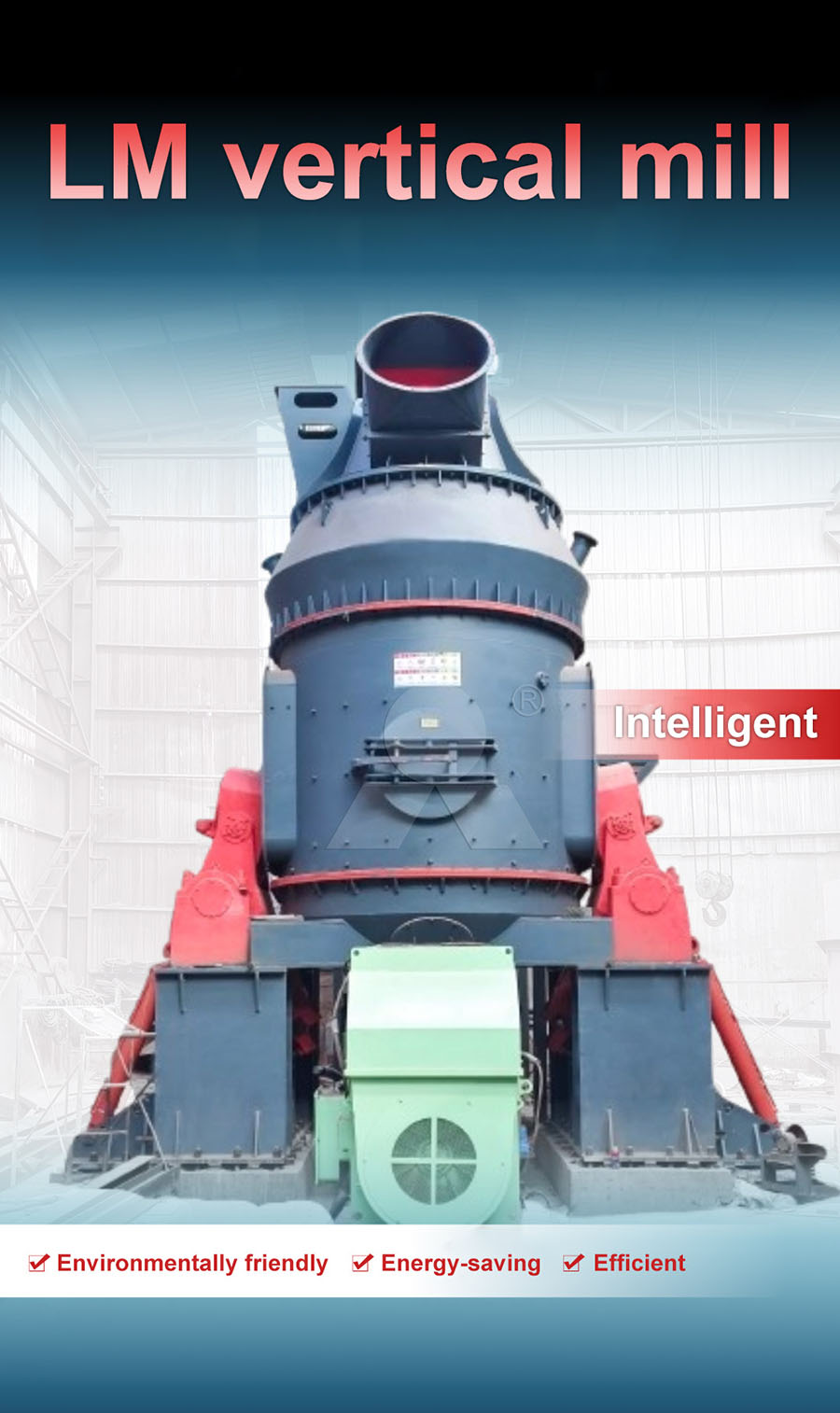
1. Leading technology and low investment cost
Integrating crushing, grinding, drying, powder selection and transportation in one, with a compact layout and can be arranged in the open air, which greatly reduces the investment cost.
2. High grinding efficiency and good product quality
The special grinding roller and grinding disc structure design has high grinding efficiency; the finished product particle size distribution is uniform and the finished product powder quality is good.
3. Reliable quality and stable operation
The grinding roller is equipped with a limit device to avoid direct contact between the grinding roller and the grinding disc, and the vibration is small; it has an automatic slag discharge function to ensure the safe operation of the equipment.
4. Large drying capacity and wide adaptability
Hot air can be used to convey materials, and materials with a moisture content of up to 15% entering the mill can be dried, and the moisture content of the materials leaving the mill is <1%, which has a wide range of adaptability.
5. High degree of automation
The automatic control system can realize remote control, interlocking protection, reliable operation and easy operation.
6. Easy maintenance and low operating cost
The grinding roller adopts forced thin oil lubrication and is equipped with a hydraulic roller turning device. During maintenance, the grinding roller can be turned out of the machine by the hydraulic device without disassembly, which is convenient and quick.
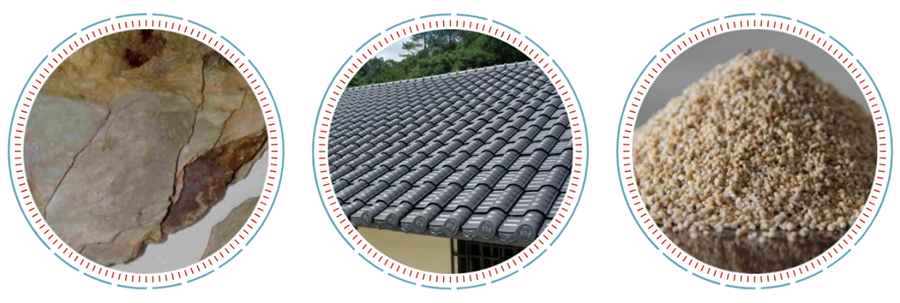
The user is a large domestic ceramic production enterprise. It focuses on the application of shale and silica sand powder in the ceramic industry, which has far-reaching significance for promoting the development of the ceramic industry and improving product quality. Liming Heavy Industry is fully responsible for planning and designing the entire production line to ensure that the layout of the production site is reasonable and compact.
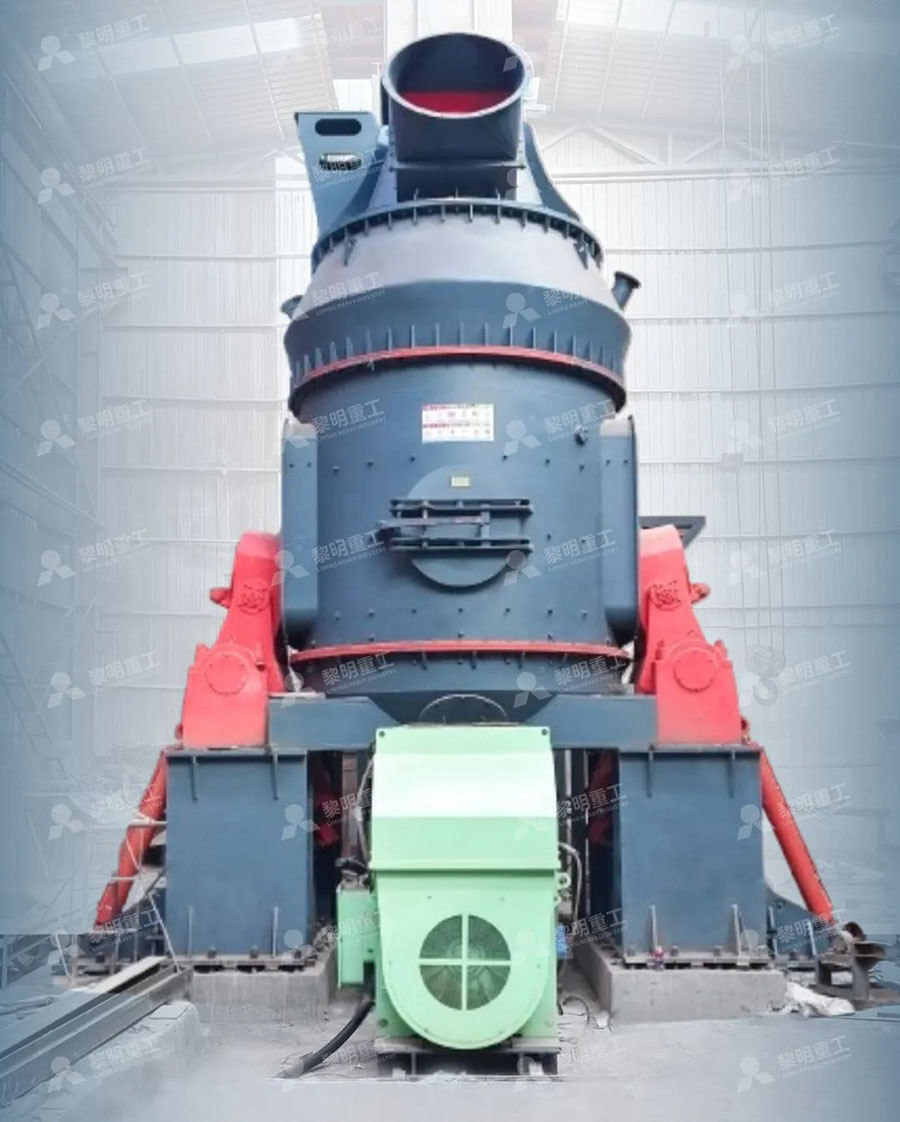
Processing materials: shale, silica sand
Finished product use: ceramics
Equipment used: LM vertical roller mill
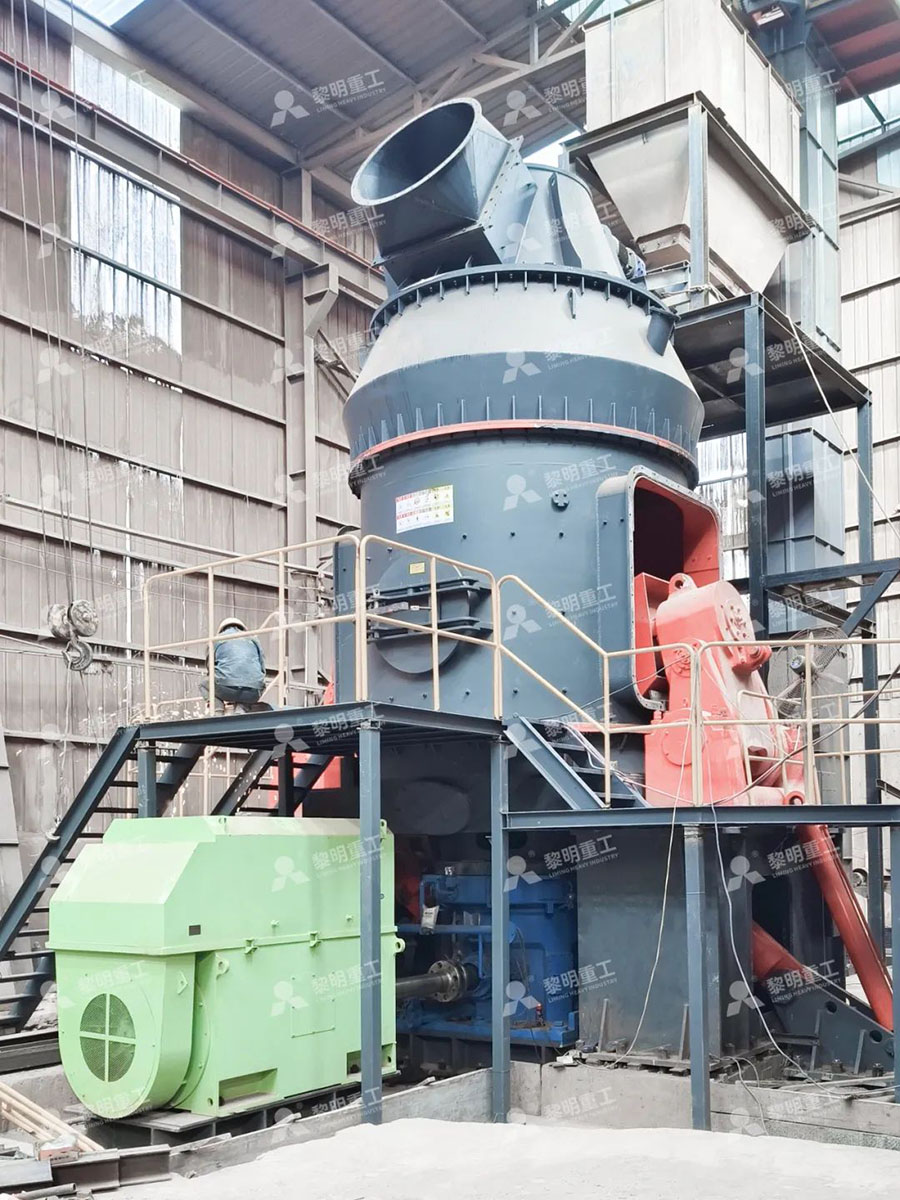
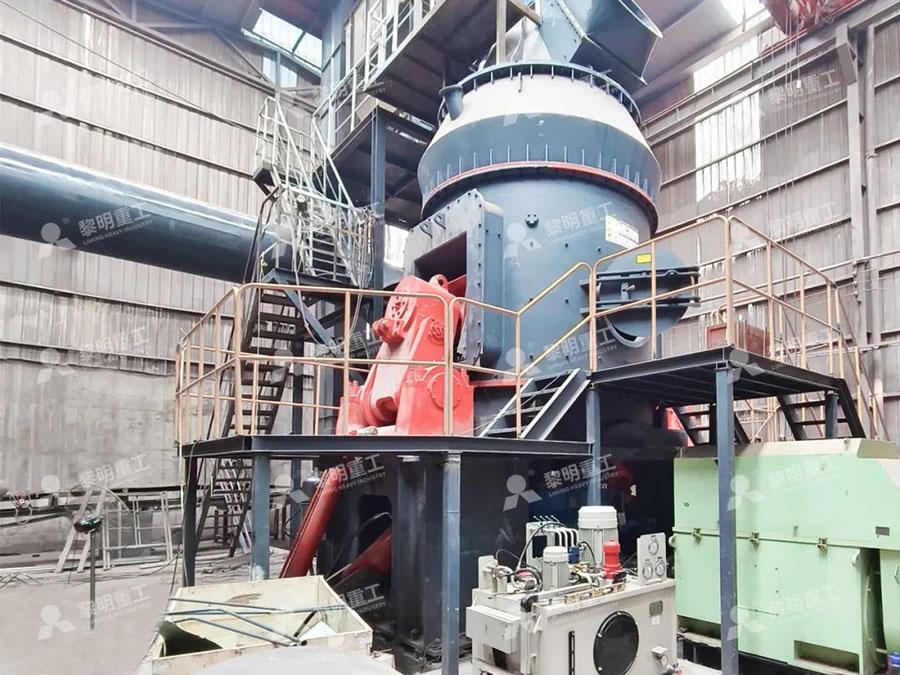
Liming Heavy Industry LM vertical roller mill integrates grinding, drying, powder selection and transportation. It meets the high standard requirements of material grinding. It can not only achieve high product purity and precise particle size control, but also save energy and reduce consumption, and has a high degree of intelligence. It can produce stably and continuously for 24 hours. Users can make diversified choices according to production, fineness, investment and other requirements.
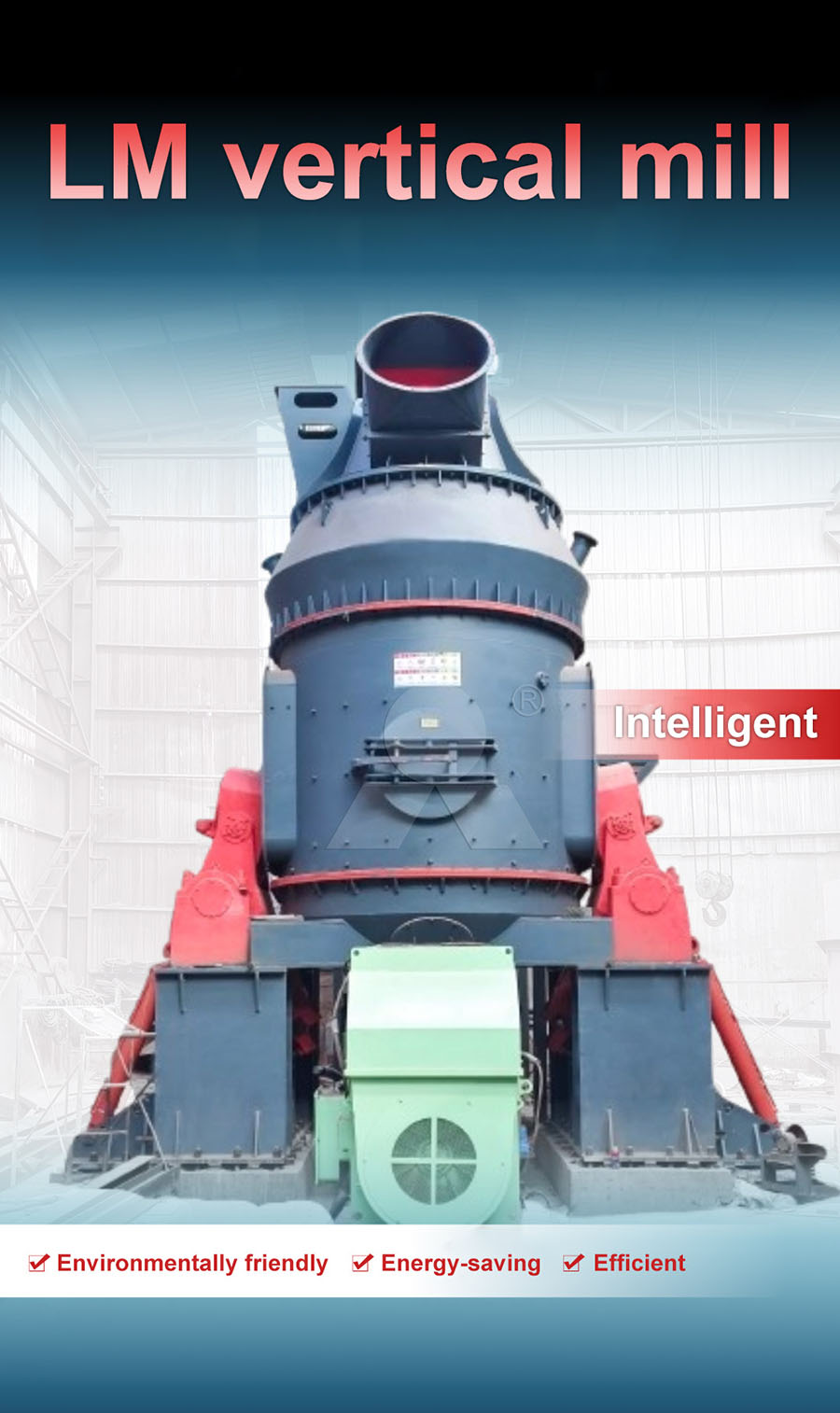
1. Leading technology and low investment cost
Integrating crushing, grinding, drying, powder selection and transportation in one, with a compact layout and can be arranged in the open air, which greatly reduces the investment cost.
2. High grinding efficiency and good product quality
The special grinding roller and grinding disc structure design has high grinding efficiency; the finished product particle size distribution is uniform and the finished product powder quality is good.
3. Reliable quality and stable operation
The grinding roller is equipped with a limit device to avoid direct contact between the grinding roller and the grinding disc, and the vibration is small; it has an automatic slag discharge function to ensure the safe operation of the equipment.
4. Large drying capacity and wide adaptability
Hot air can be used to convey materials, and materials with a moisture content of up to 15% entering the mill can be dried, and the moisture content of the materials leaving the mill is <1%, which has a wide range of adaptability.
5. High degree of automation
The automatic control system can realize remote control, interlocking protection, reliable operation and easy operation.
6. Easy maintenance and low operating cost
The grinding roller adopts forced thin oil lubrication and is equipped with a hydraulic roller turning device. During maintenance, the grinding roller can be turned out of the machine by the hydraulic device without disassembly, which is convenient and quick.