Liming Heavy Industry focuses on rare earth material recycling projects
Introduction to rare earth resources:
As a general term for 17 metal elements including lanthanide, scandium and yttrium, rare earths are divided into two strategic reserves: light rare earths and medium and heavy rare earths based on atomic weight differences. Its compounds play an irreplaceable role in cutting-edge fields such as new energy power systems and robot precision transmission; they also support the research and development of super materials for national defense equipment such as missile inertial navigation systems and satellite payload components.
Light rare earths:
Lanthanum (La), cerium (Ce), praseodymium (Pr), neodymium (Nd), promethium (Pm)
Medium and heavy rare earths:
Samarium (Sm), europium (Eu), gadolinium (Gd)
Terbium (Tb), distillation (Dy), holmium (Ho)
Erbium (Er), thulium (Tm), ytterbium (Yb).
Lutetium (Lu), scandium (Sc), yttrium (Y)
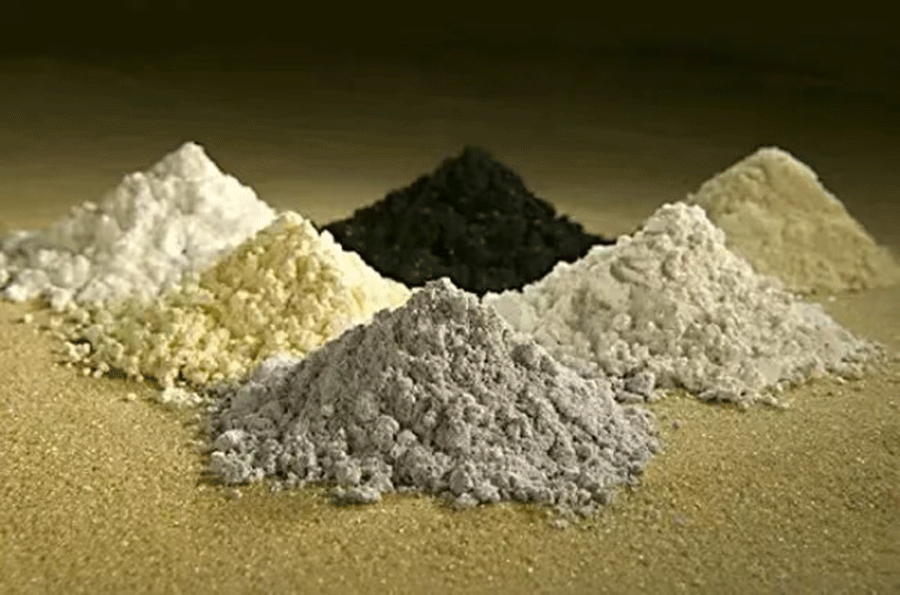
Rare earth industry chain:
Mining and beneficiation
Smelting and separation
Material preparation
Terminal application
Recycling
Main sources of rare earth secondary resources:
1. Rare earth molten salt slag
Under the general trend of the transformation of the rare earth industry towards high-end and refined production, rare earth molten salt electrolysis has become a key technology in the field of rare earth smelting with its advantage of being able to efficiently produce rare earth metals, providing important support for the development of cutting-edge industries such as new energy vehicles and semiconductors. However, due to factors such as electrode reactions and temperature fluctuations during the electrolysis process, the generation of rare earth molten salt slag is difficult to avoid. Although the enrichment of rare earth elements in this type of molten salt slag is limited, its total amount is huge. Through effective recycling and treatment, a considerable amount of rare earth elements can still be extracted to achieve resource reuse.
Rare earth molten salt electrolysis preparation and molten salt slag recovery process:
Rare earth--rare earth compounds--molten salt electrolysis--rare earth metals--by-product rare earth molten salt slag--secondary recovery
2. NdFeB waste
Rare earth family "magnetic elements" such as neodymium, praseodymium, and dysprosium are becoming the strategic fulcrum of this green revolution--the NdFeB permanent magnet materials synthesized from them, with the highest magnetic energy product and energy conversion efficiency, have become the "heart components" of new energy vehicle motors and wind turbines.
With the outbreak of the global new energy industry, a huge wave of scrapped magnetic materials is approaching--China alone produces more than 50,000 tons of NdFeB scraps, waste motors and other "urban mines" each year, with a rare earth content of up to 30%-35%, far exceeding the grade of primary ore (3%-5%). How to efficiently extract strategic resources from these "invisible gold mines" will become the key to victory in the second half of the rare earth war.
Generation of NdFeB waste:
Raw material preparation
Various single raw material losses will be generated during raw material pretreatment, such as metal neodymium, pure iron, ferroboron, metal dysprosium, cobalt, etc.
Smelting, casting
Oxide scale will be generated during the smelting and casting process, which is a severely oxidized NdFeB waste.
Crushing, powder making
Ultrafine powder (particle size below 2um) generated during the powder making process and magnetic powder that catches fire due to exposure to air.
Orientation, pressing
Alloy powder scattered during magnetic field forming.
Sintering, tempering
Some slightly oxidized NdFeB block waste will be generated during the sintering process.
Machining
Grinding powder, large A large amount of scraps and waste materials damaged by processing.
Surface treatment
Surface treatment defective products
Finished product inspection
Finished product inspection defective products
Finished product scrapping
Scrapped motor dismantling waste strong magnet
Rare earth resource recycling process:
NdFeB waste industrial recycling process (oxidation roasting-hydrochloric acid solution method)
Raw material entry---oxidation roasting---grinding---hydrochloric acid decomposition---impurity removal---extraction---oxide solution---precipitation---burning---successful acquisition
Grinding equipment selection:
Based on nearly 40 years of research and development of grinding equipment, Liming Heavy Industry has innovatively applied core equipment such as MTW European version grinding mill and LM vertical roller mill to the field of rare earth recycling, providing professional solutions for the efficient reuse of NdFeB waste and molten salt slag. In view of the complex composition of rare earth recycling materials, diverse element occurrence forms, and high threshold of purification process, Liming Heavy Industry's equipment has demonstrated significant technical advantages. It can not only achieve efficient grinding and precise control of particle size to greatly improve the rare earth recovery rate, but also has the characteristics of intelligent energy saving and green environmental protection, effectively reducing energy consumption and pollution.
LM series vertical roller mill
Finished product fineness range: 20-400 mesh (0.84-0.038mm)
1. Simple operation, reliable operation
2. Negative pressure operation, green and environmentally friendly
3. Low energy consumption, low wear
4. High drying efficiency, automatic slag discharge
5. High grinding efficiency, high finished product quality
6. Small footprint, low investment cost
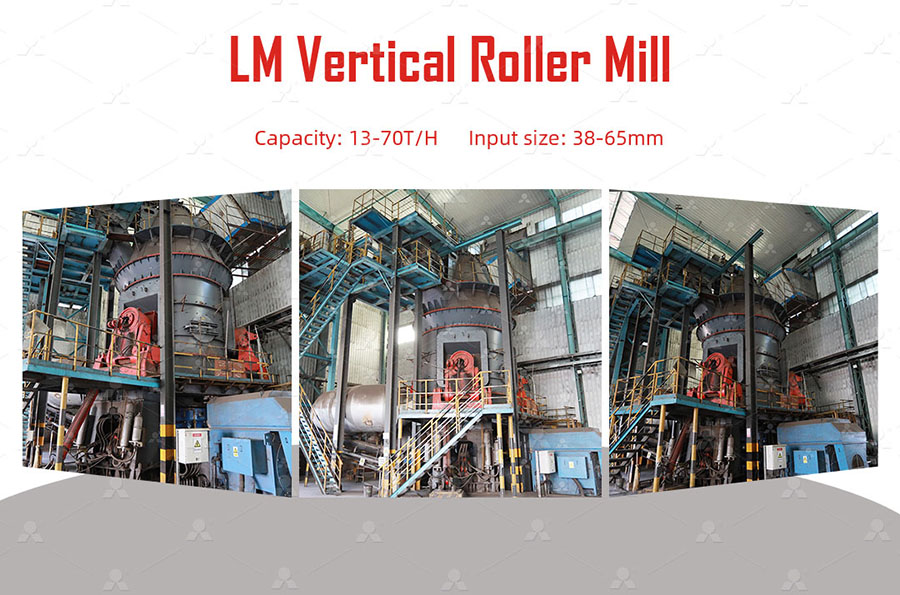
Working principle and process flow:
The motor drives the reducer to drive the grinding disc to rotate. The material to be ground is fed into the center of the rotating grinding disc by the air-locking feeding device. Under the action of centrifugal force, the material moves to the periphery of the grinding disc and enters the grinding roller. Under the pressure of the grinding roller, the material is crushed by extrusion, grinding and shearing. At the same time, hot air is evenly ejected upward from the wind ring surrounding the grinding disc at high speed. The ground material is blown up by the high-speed airflow at the wind ring. On the one hand, the coarser material is blown back to the grinding disc for re-grinding, and on the other hand, the suspended material is dried. The fine powder is brought into the separator by the hot air for classification. The qualified fine powder is discharged from the mill along with the air flow and collected by the dust collection equipment as the product. The unqualified coarse powder falls back to the grinding disc under the action of the separator blades and is re-grinded with the newly fed material. This cycle completes the entire grinding process.
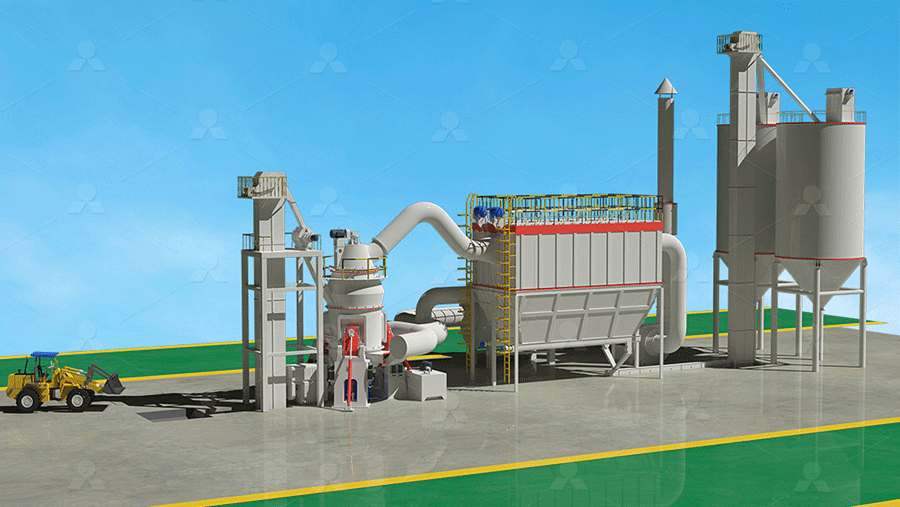
MTW series European version grinding mill
Finished product fineness range: 12-325 days (1.6-0.045mm), the finest can reach 400 mesh
1. Simple operation, reliable operation
2. Convenient maintenance, low operating cost
3. Bevel gear transmission, stable operation
4. Economical investment, green and environmentally friendly
5. Not easy to block, high powder selection efficiency
6. Integrated comprehensive solution
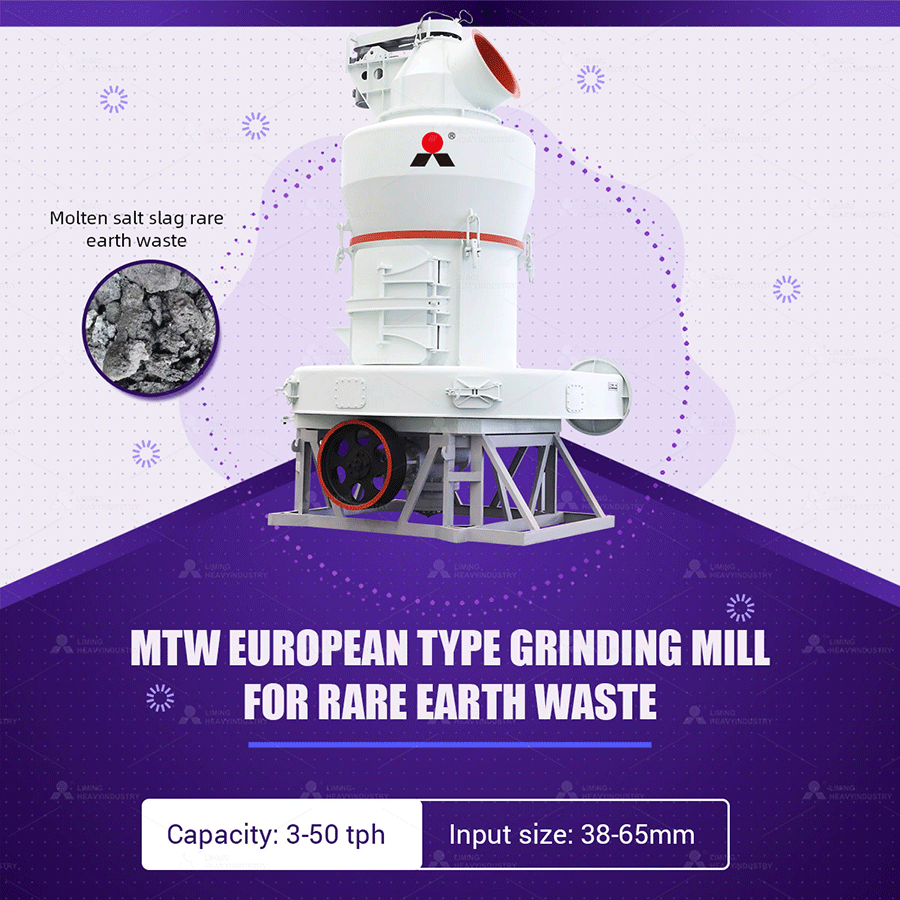
Working principle and process flow:
The raw materials are evenly and quantitatively fed into the main engine room for grinding by the variable frequency belt feeder. The ground materials are sent into the powder selector by the fan airflow for classification. Under the action of the analyzer, the materials that do not meet the fineness requirements fall into the grinding room for re-grinding, and the qualified materials are followed by the airflow through the pipeline into the cyclone powder collector for separation and collection, and the finished powder is discharged through the discharge device. The separated airflow enters the fan through the return air duct at the upper end of the cyclone powder collector. The production system operates under negative pressure and closed conditions, and is equipped with a pulse dust collector without dust spillage, which meets national environmental protection standards.
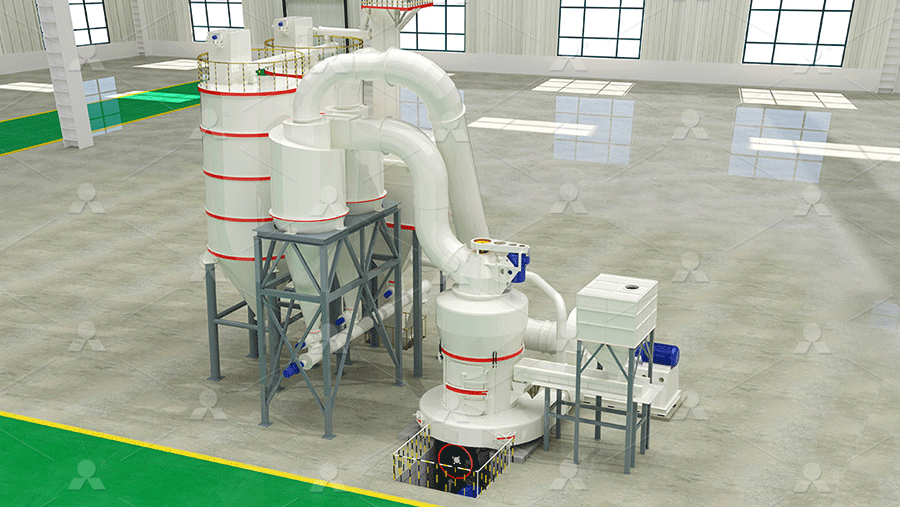
Case:
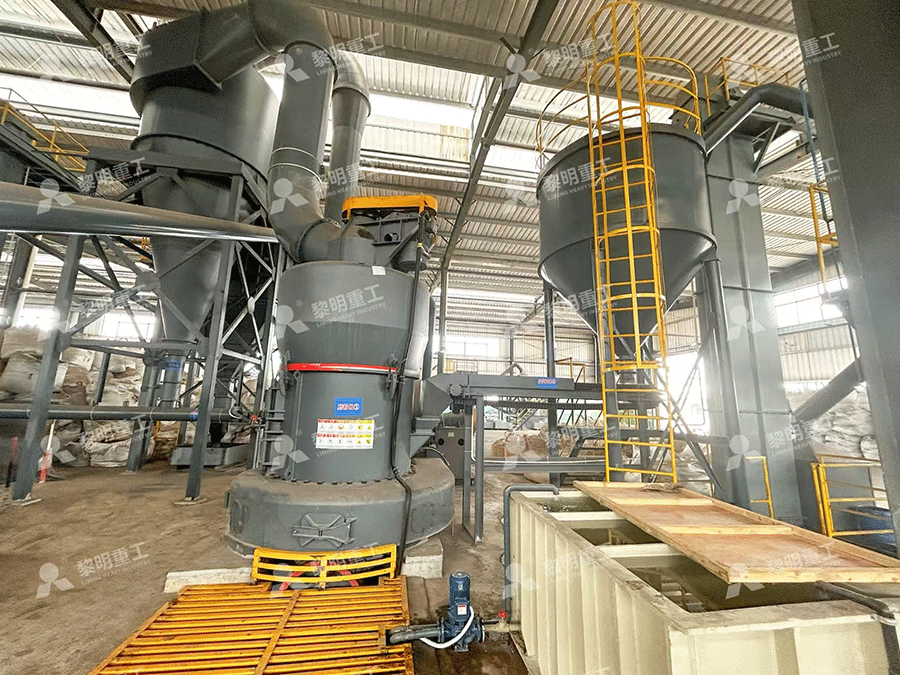
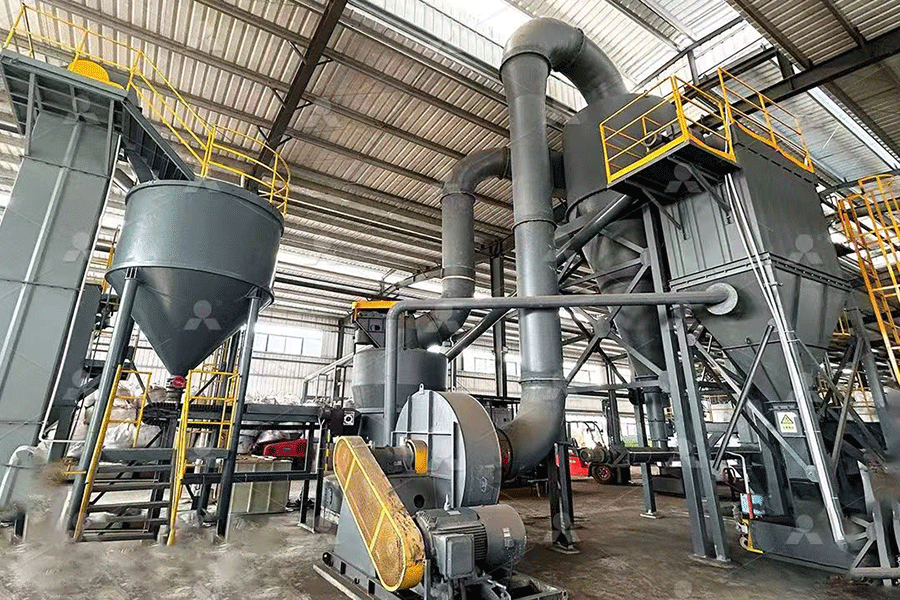
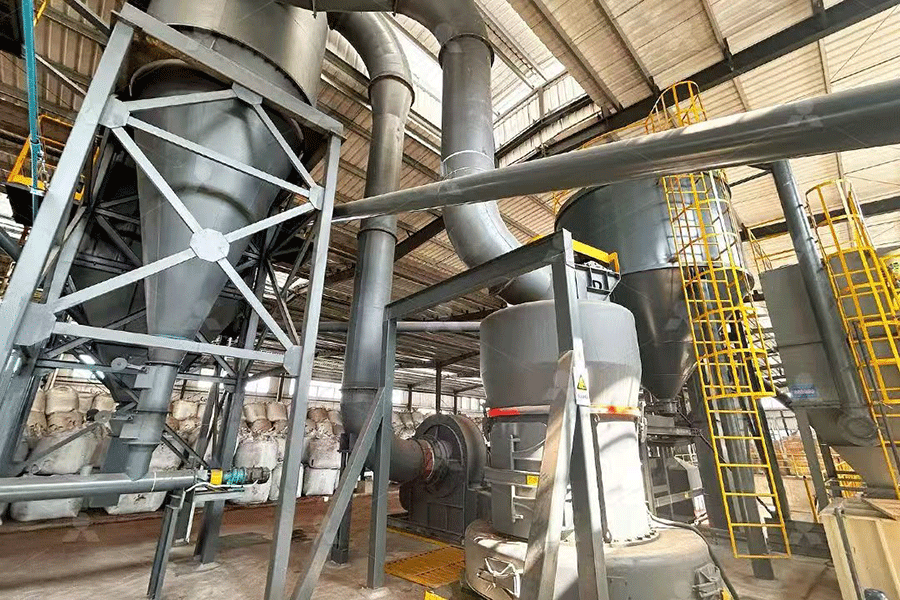
As a general term for 17 metal elements including lanthanide, scandium and yttrium, rare earths are divided into two strategic reserves: light rare earths and medium and heavy rare earths based on atomic weight differences. Its compounds play an irreplaceable role in cutting-edge fields such as new energy power systems and robot precision transmission; they also support the research and development of super materials for national defense equipment such as missile inertial navigation systems and satellite payload components.
Light rare earths:
Lanthanum (La), cerium (Ce), praseodymium (Pr), neodymium (Nd), promethium (Pm)
Medium and heavy rare earths:
Samarium (Sm), europium (Eu), gadolinium (Gd)
Terbium (Tb), distillation (Dy), holmium (Ho)
Erbium (Er), thulium (Tm), ytterbium (Yb).
Lutetium (Lu), scandium (Sc), yttrium (Y)
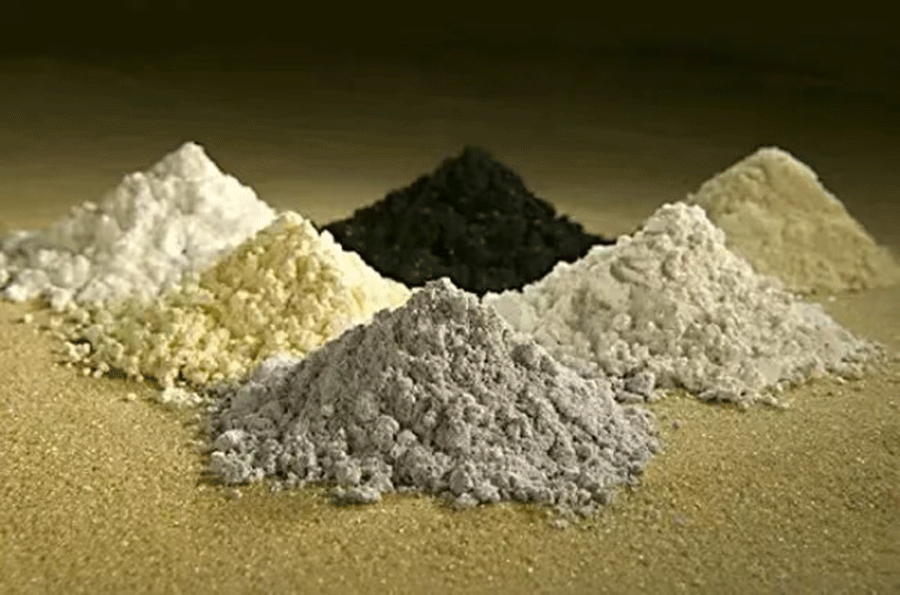
Rare earth industry chain:
Mining and beneficiation
Smelting and separation
Material preparation
Terminal application
Recycling
Main sources of rare earth secondary resources:
1. Rare earth molten salt slag
Under the general trend of the transformation of the rare earth industry towards high-end and refined production, rare earth molten salt electrolysis has become a key technology in the field of rare earth smelting with its advantage of being able to efficiently produce rare earth metals, providing important support for the development of cutting-edge industries such as new energy vehicles and semiconductors. However, due to factors such as electrode reactions and temperature fluctuations during the electrolysis process, the generation of rare earth molten salt slag is difficult to avoid. Although the enrichment of rare earth elements in this type of molten salt slag is limited, its total amount is huge. Through effective recycling and treatment, a considerable amount of rare earth elements can still be extracted to achieve resource reuse.
Rare earth molten salt electrolysis preparation and molten salt slag recovery process:
Rare earth--rare earth compounds--molten salt electrolysis--rare earth metals--by-product rare earth molten salt slag--secondary recovery
2. NdFeB waste
Rare earth family "magnetic elements" such as neodymium, praseodymium, and dysprosium are becoming the strategic fulcrum of this green revolution--the NdFeB permanent magnet materials synthesized from them, with the highest magnetic energy product and energy conversion efficiency, have become the "heart components" of new energy vehicle motors and wind turbines.
With the outbreak of the global new energy industry, a huge wave of scrapped magnetic materials is approaching--China alone produces more than 50,000 tons of NdFeB scraps, waste motors and other "urban mines" each year, with a rare earth content of up to 30%-35%, far exceeding the grade of primary ore (3%-5%). How to efficiently extract strategic resources from these "invisible gold mines" will become the key to victory in the second half of the rare earth war.
Generation of NdFeB waste:
Raw material preparation
Various single raw material losses will be generated during raw material pretreatment, such as metal neodymium, pure iron, ferroboron, metal dysprosium, cobalt, etc.
Smelting, casting
Oxide scale will be generated during the smelting and casting process, which is a severely oxidized NdFeB waste.
Crushing, powder making
Ultrafine powder (particle size below 2um) generated during the powder making process and magnetic powder that catches fire due to exposure to air.
Orientation, pressing
Alloy powder scattered during magnetic field forming.
Sintering, tempering
Some slightly oxidized NdFeB block waste will be generated during the sintering process.
Machining
Grinding powder, large A large amount of scraps and waste materials damaged by processing.
Surface treatment
Surface treatment defective products
Finished product inspection
Finished product inspection defective products
Finished product scrapping
Scrapped motor dismantling waste strong magnet
Rare earth resource recycling process:
NdFeB waste industrial recycling process (oxidation roasting-hydrochloric acid solution method)
Raw material entry---oxidation roasting---grinding---hydrochloric acid decomposition---impurity removal---extraction---oxide solution---precipitation---burning---successful acquisition
Grinding equipment selection:
Based on nearly 40 years of research and development of grinding equipment, Liming Heavy Industry has innovatively applied core equipment such as MTW European version grinding mill and LM vertical roller mill to the field of rare earth recycling, providing professional solutions for the efficient reuse of NdFeB waste and molten salt slag. In view of the complex composition of rare earth recycling materials, diverse element occurrence forms, and high threshold of purification process, Liming Heavy Industry's equipment has demonstrated significant technical advantages. It can not only achieve efficient grinding and precise control of particle size to greatly improve the rare earth recovery rate, but also has the characteristics of intelligent energy saving and green environmental protection, effectively reducing energy consumption and pollution.
LM series vertical roller mill
Finished product fineness range: 20-400 mesh (0.84-0.038mm)
1. Simple operation, reliable operation
2. Negative pressure operation, green and environmentally friendly
3. Low energy consumption, low wear
4. High drying efficiency, automatic slag discharge
5. High grinding efficiency, high finished product quality
6. Small footprint, low investment cost
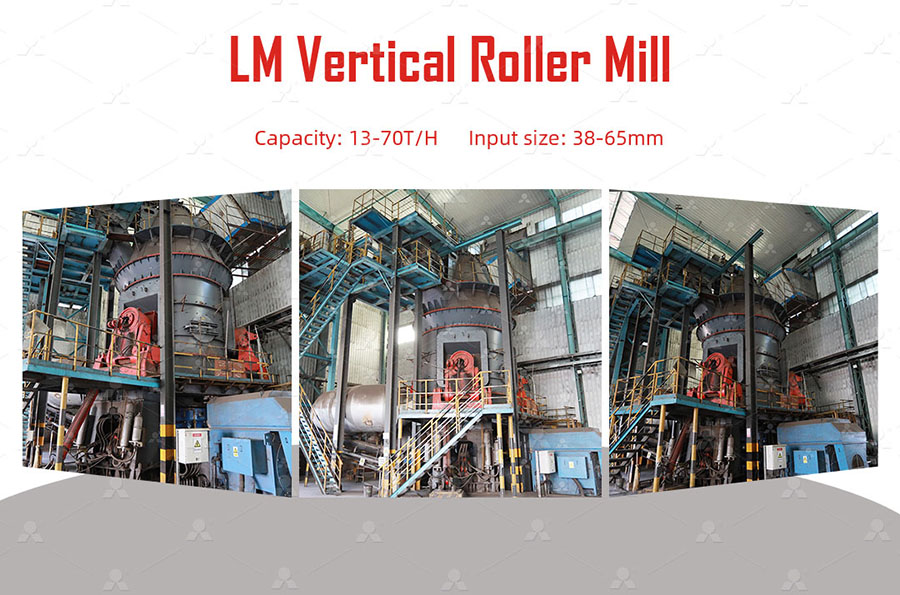
Working principle and process flow:
The motor drives the reducer to drive the grinding disc to rotate. The material to be ground is fed into the center of the rotating grinding disc by the air-locking feeding device. Under the action of centrifugal force, the material moves to the periphery of the grinding disc and enters the grinding roller. Under the pressure of the grinding roller, the material is crushed by extrusion, grinding and shearing. At the same time, hot air is evenly ejected upward from the wind ring surrounding the grinding disc at high speed. The ground material is blown up by the high-speed airflow at the wind ring. On the one hand, the coarser material is blown back to the grinding disc for re-grinding, and on the other hand, the suspended material is dried. The fine powder is brought into the separator by the hot air for classification. The qualified fine powder is discharged from the mill along with the air flow and collected by the dust collection equipment as the product. The unqualified coarse powder falls back to the grinding disc under the action of the separator blades and is re-grinded with the newly fed material. This cycle completes the entire grinding process.
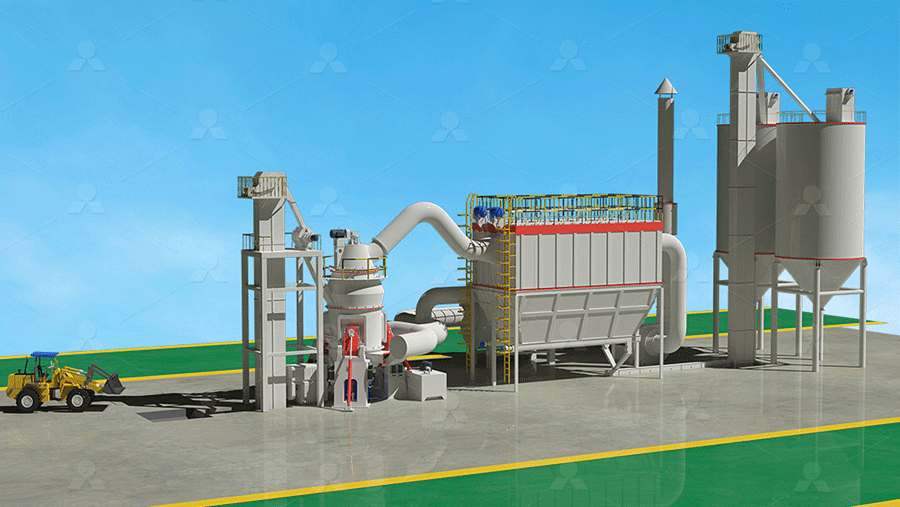
MTW series European version grinding mill
Finished product fineness range: 12-325 days (1.6-0.045mm), the finest can reach 400 mesh
1. Simple operation, reliable operation
2. Convenient maintenance, low operating cost
3. Bevel gear transmission, stable operation
4. Economical investment, green and environmentally friendly
5. Not easy to block, high powder selection efficiency
6. Integrated comprehensive solution
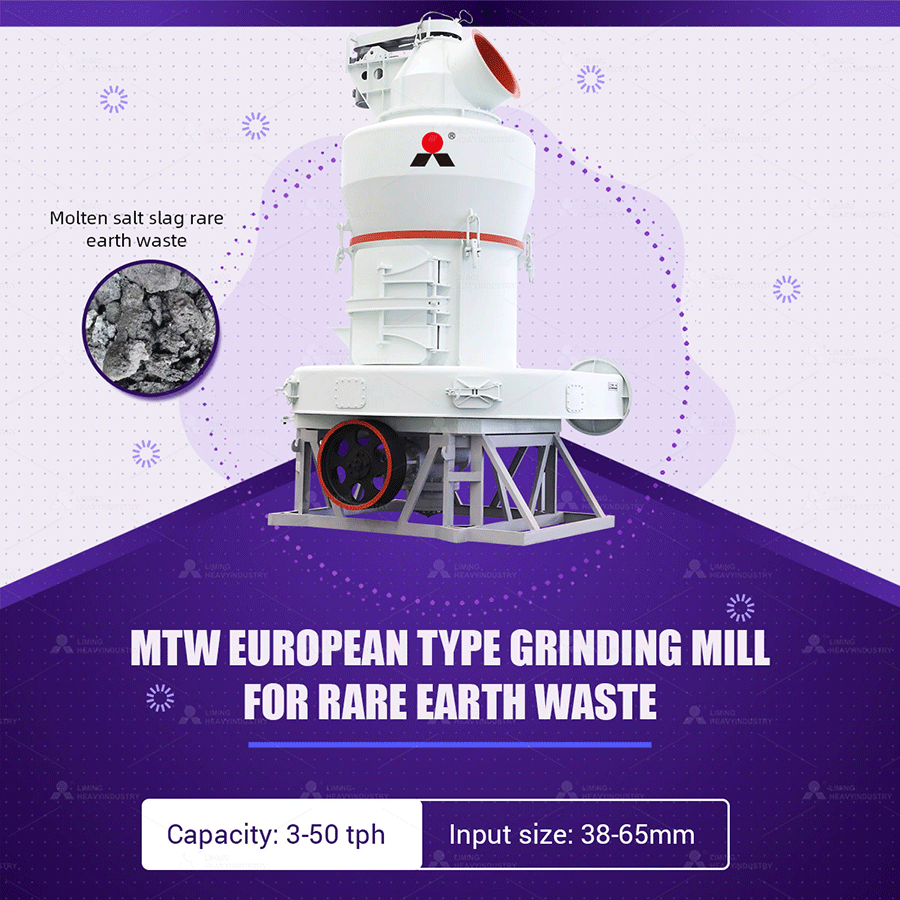
Working principle and process flow:
The raw materials are evenly and quantitatively fed into the main engine room for grinding by the variable frequency belt feeder. The ground materials are sent into the powder selector by the fan airflow for classification. Under the action of the analyzer, the materials that do not meet the fineness requirements fall into the grinding room for re-grinding, and the qualified materials are followed by the airflow through the pipeline into the cyclone powder collector for separation and collection, and the finished powder is discharged through the discharge device. The separated airflow enters the fan through the return air duct at the upper end of the cyclone powder collector. The production system operates under negative pressure and closed conditions, and is equipped with a pulse dust collector without dust spillage, which meets national environmental protection standards.
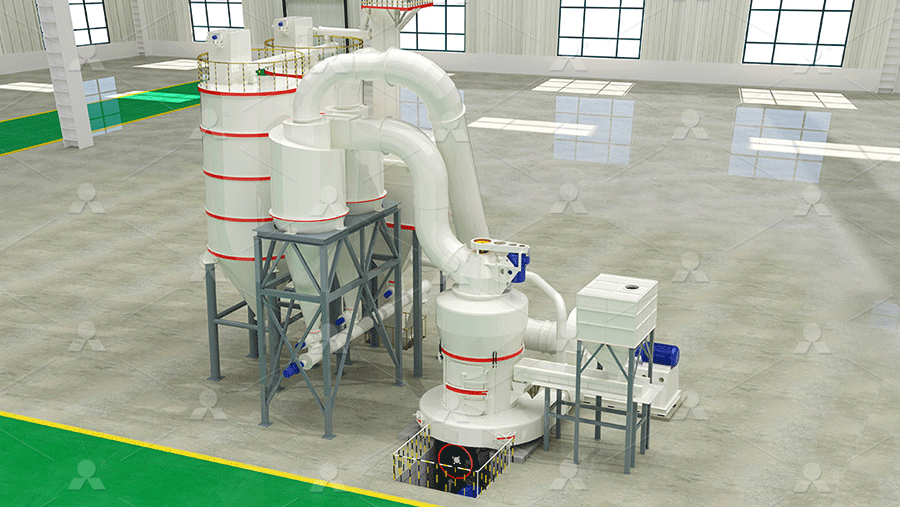
Case:
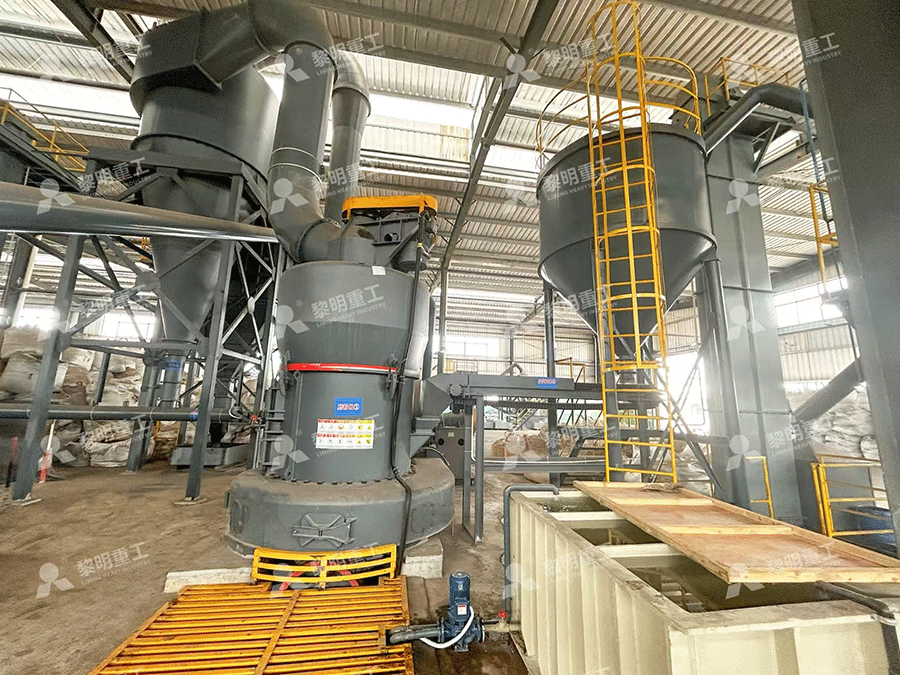
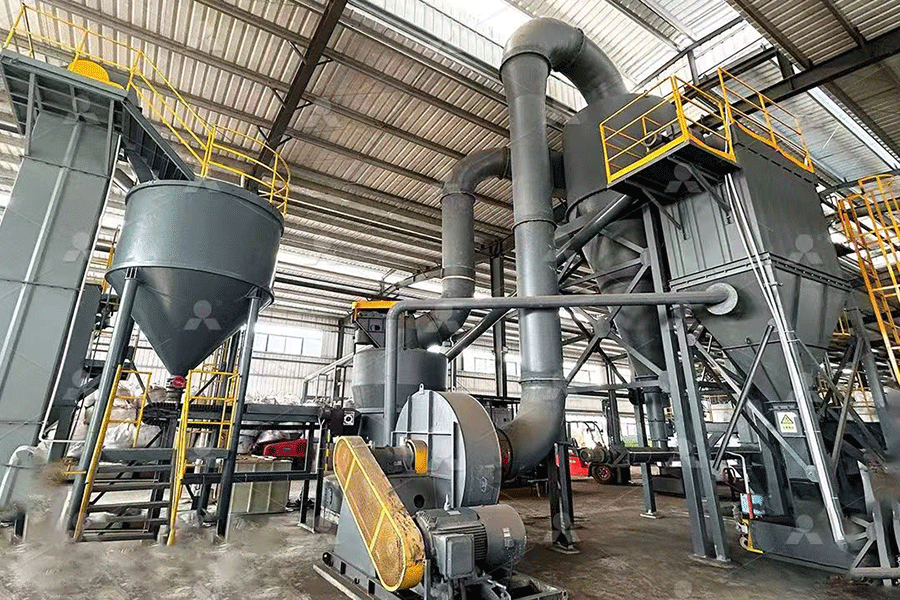
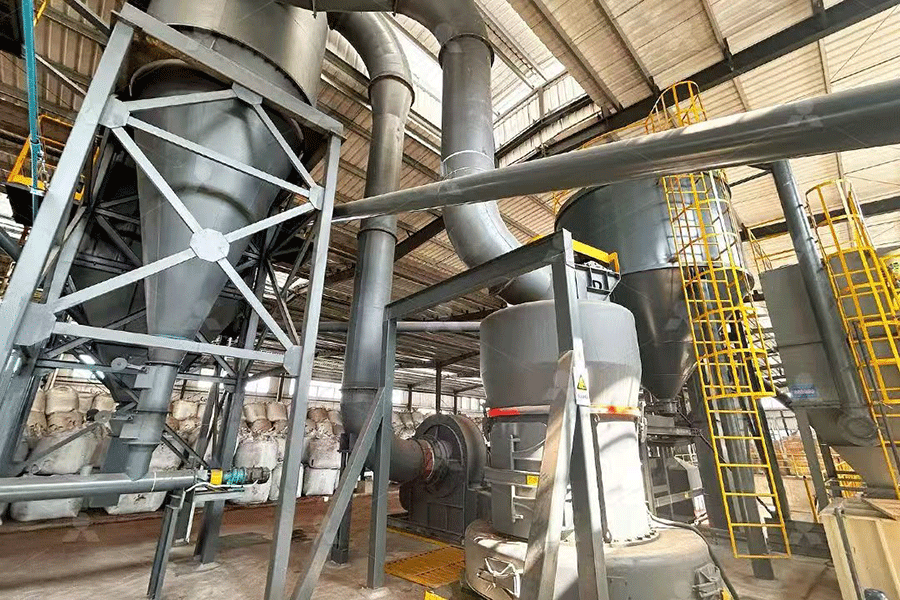