MTW European version grinding mill assists secondary aluminum ash powder making project
Aluminum ash is a hazardous waste that is inevitably produced in all aluminum smelting links such as primary aluminum production, aluminum processing, and waste aluminum recycling.
Project overview:
Against the background of rapid expansion of aluminum industry, the environmental hazards brought by secondary aluminum ash are becoming increasingly prominent - problems such as release of toxic gases, salt and fluoride infiltration pollution when in contact with water, making traditional landfill or incineration disposal face the dual dilemma of environmental protection and economy. This project reconstructs the aluminum ash treatment path through wet regeneration technology, forming a "hazardous waste → water purifier → resource regeneration" cycle chain, and realizing the full quantitative recycling of aluminum ash. It has been successfully implemented and put into production in the local area. In the preparation stage of the project, the client conducted rigorous research and strict evaluation, and selected the MTW European version grinding mill of Liming Heavy Industry, breaking through the technical pain points of low acid decomposition efficiency and high energy consumption caused by uneven aluminum ash particle size in traditional processes, significantly improving resource recovery efficiency, reducing processing energy consumption, and providing a replicable technical solution for the green transformation of the aluminum industry and the construction of a "zero-waste city".
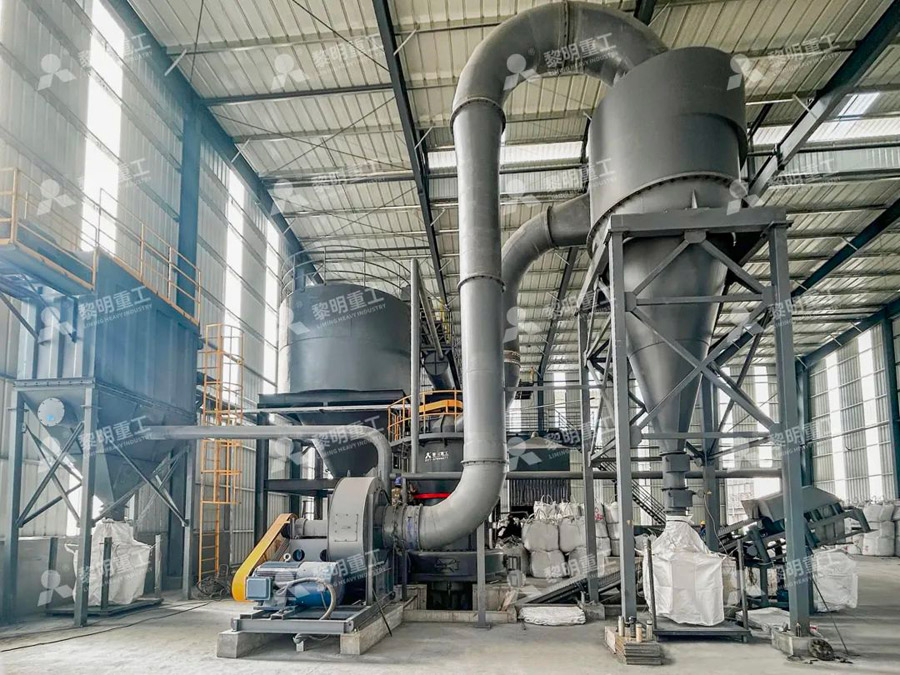
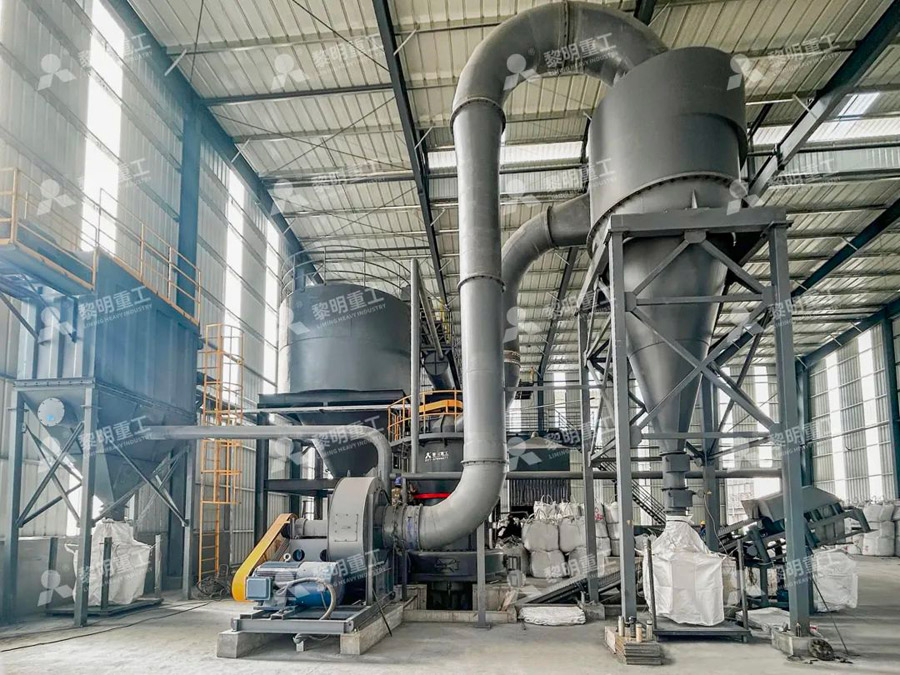
Processing materials: secondary aluminum ash
Finished product use: as raw material for the production of aluminum chloride series water purifiers
Equipment used: MTW series European version mill
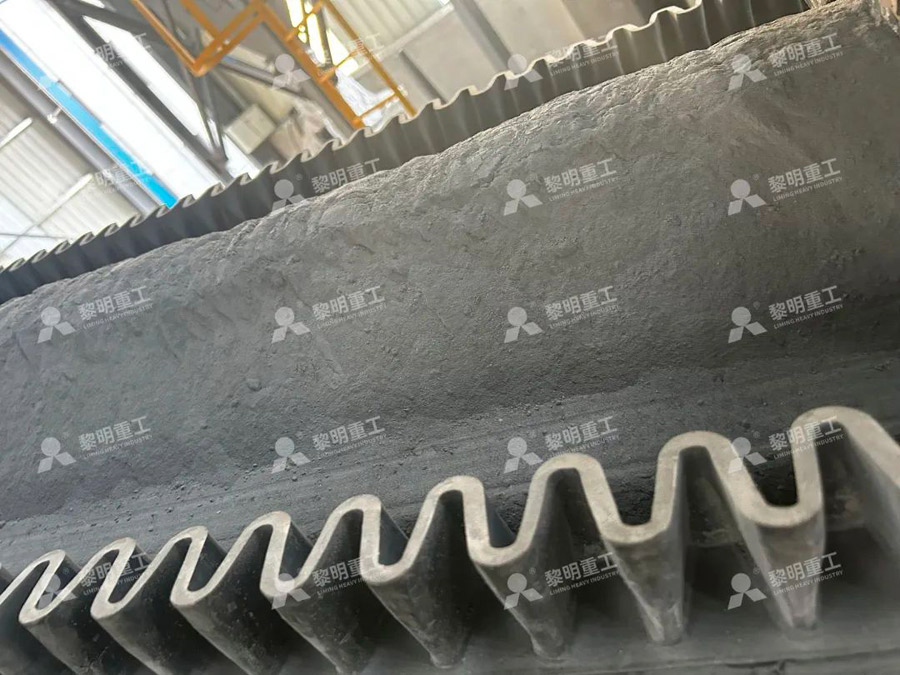
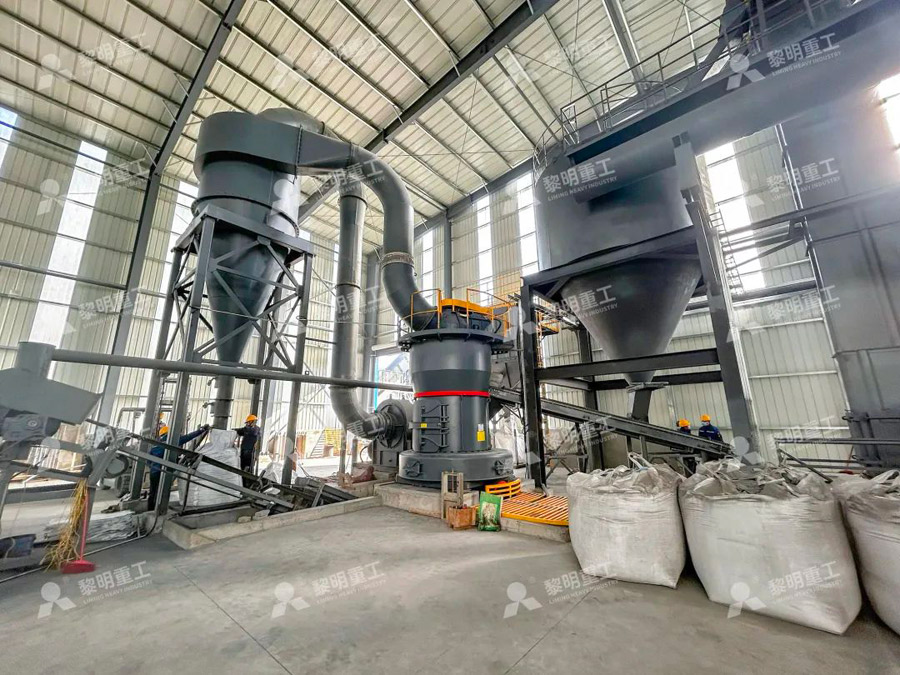
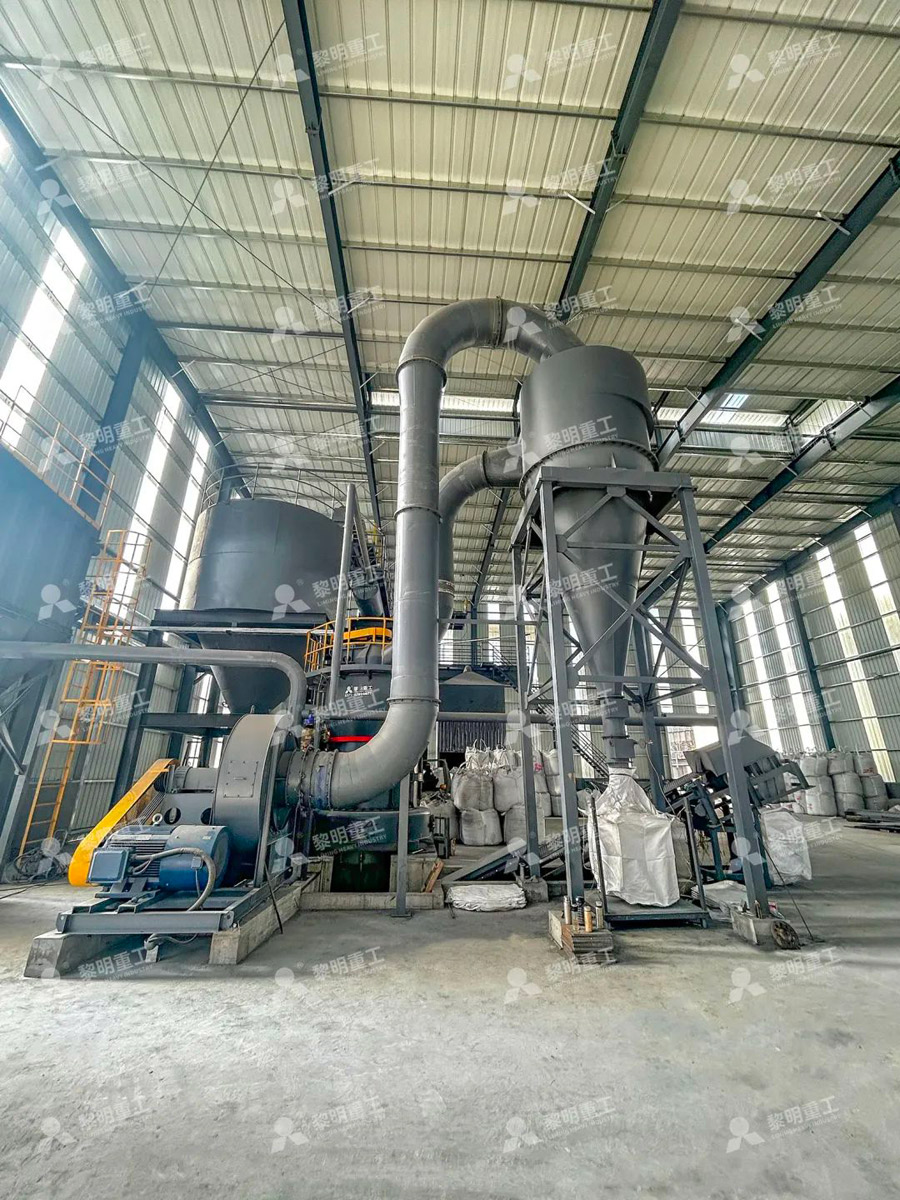
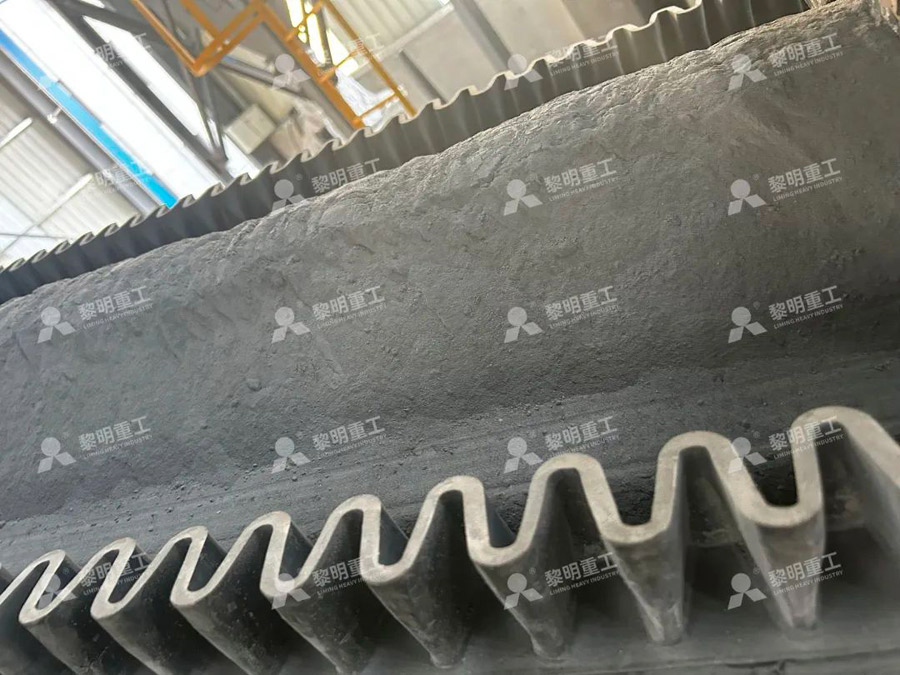
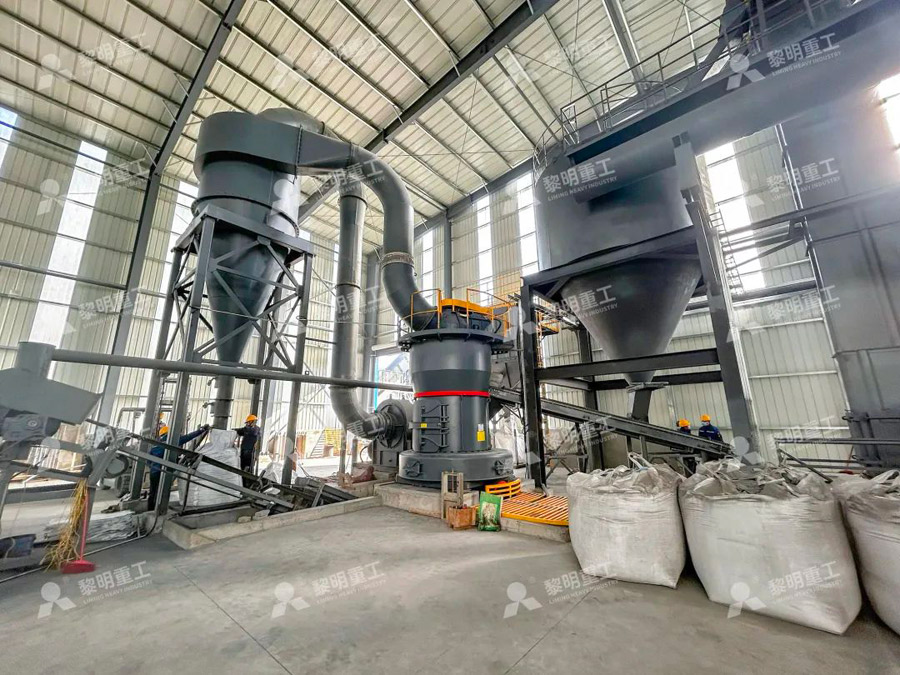
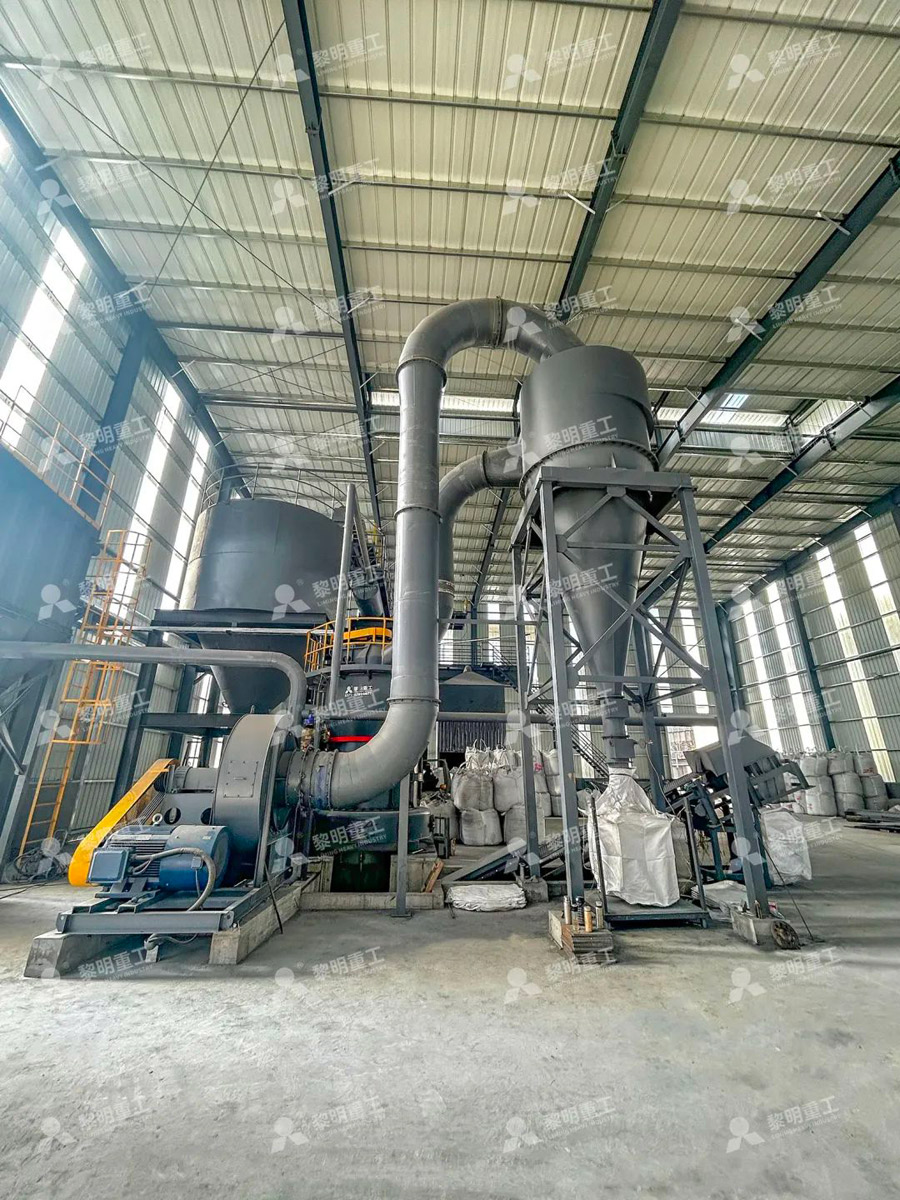
Process flow of aluminum ash to prepare aluminum chloride water purifier:
Primary aluminum ash--primary aluminum extraction--secondary aluminum ash--MTW European version grinding mill--chemical leaching--solid-liquid separation--regulation and polymerization--drying and packaging
European version grinding mill powder making process:
The raw materials are uniformly and quantitatively fed into the main machine grinding chamber for grinding by the variable frequency belt feeder. The ground materials are sent to the powder selector by the fan airflow for classification. Under the action of the analyzer, the materials that do not meet the fineness requirements fall into the grinding chamber for re-grinding, and the qualified materials are followed by the airflow through the pipeline into the cyclone powder collector for separation and collection, and are discharged through the discharge device as the finished powder. The separated airflow enters the fan through the return air duct at the upper end of the cyclone powder collector. The production system operates under negative pressure and closed conditions, and is equipped with a pulse dust collector without dust spillage, which meets national environmental protection standards.
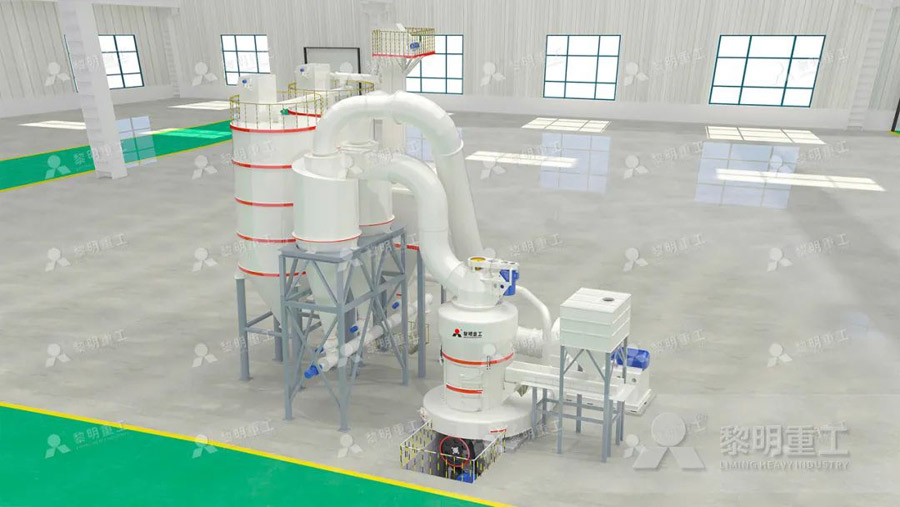
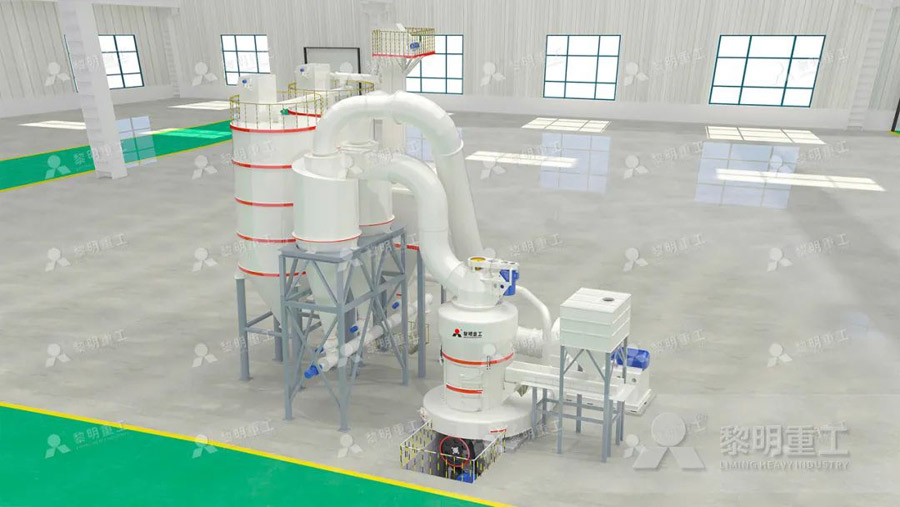
Equipment selection and advantages:
As a provider of overall solutions for grinding equipment, Liming Heavy Industry has developed and launched the MTW series European version grinding mill after nearly 40 years of deep technical cultivation and experience accumulation. This equipment plays an irreplaceable key role in the pretreatment stage of secondary aluminum ash, which has high hardness, unique toughness and complex and diverse components. It provides high-quality raw materials with highly adapted particle size for subsequent processes, and effectively improves the efficiency of resource utilization of aluminum ash hazardous waste.
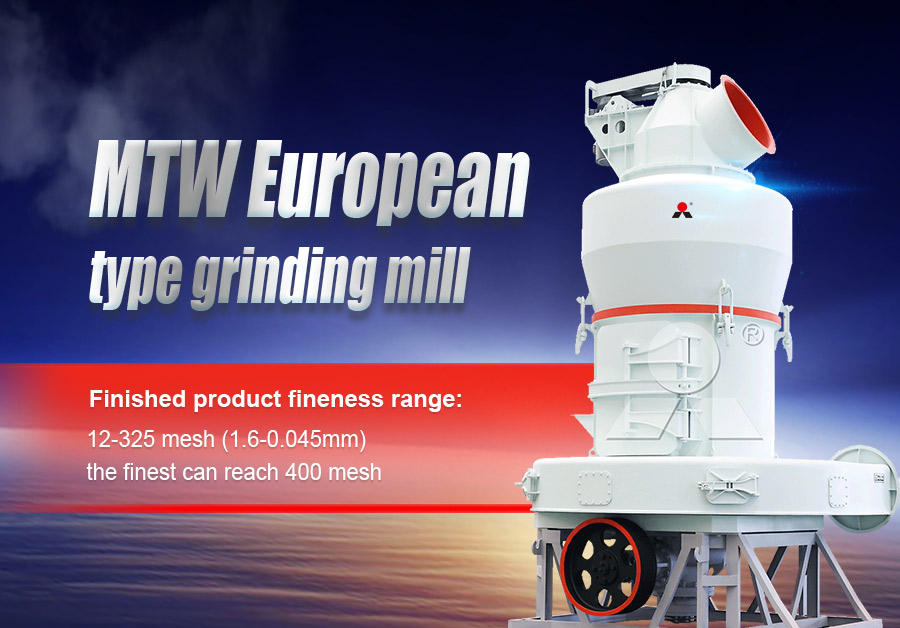
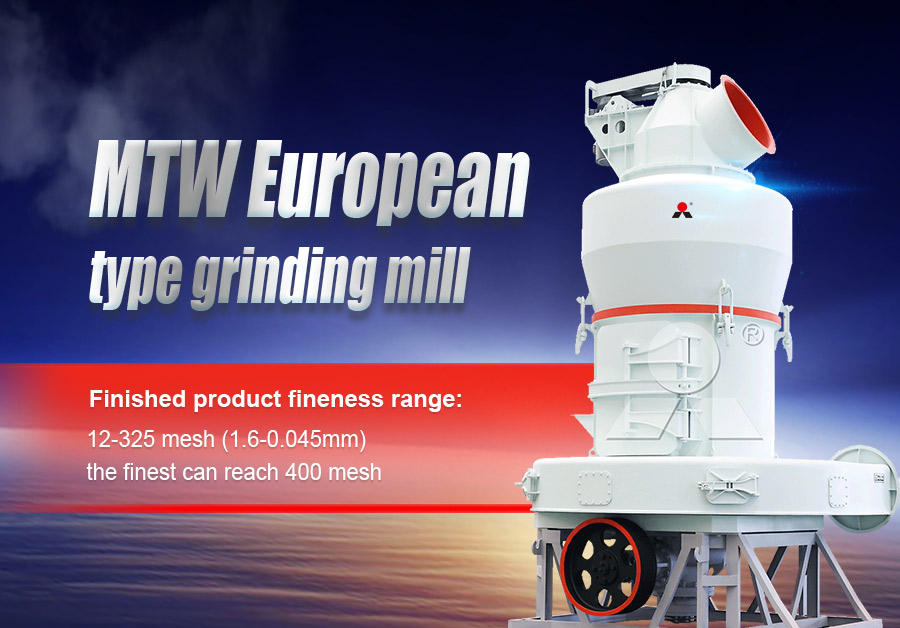
1. The equipment is mature and stable. It adopts seven core patents and has nearly 40 years of experience in mill manufacturing; the four generations of mills have matured and transformed, and it is a high-quality product in the swing mill industry.
2. The overall transmission ratio of the bevel gear is precise, the power is strong, the efficiency is high, the output is large, and the energy consumption is low. The sinking design has stable operation, low vibration and low noise.
3. The transmission system adopts thin oil lubrication. The main shaft transmission system and the fan transmission system are both lubricated with thin oil. The oil change cycle is as long as 4 months, and the maintenance frequency is low.
4. The new variable frequency powder classifier adopts a new hanging cage powder classifier, which has high powder selection efficiency, variable frequency control, and more precise fineness adjustment.
5. Economical investment, green and environmental protection, small footprint, simple structure layout, strong set-up, low infrastructure cost, short construction period, and fast capital recovery. The finished product has low pollution and high whiteness. The whole system operates under negative pressure without dust overflow, meeting the latest national environmental protection requirements.
6. Integrated comprehensive solution provides integrated comprehensive solutions such as design, supply, construction, and service, which is worry-free, safe, and assured.