LUM ultrafine vertical mill helps the ultrafine heavy calcium powder preparation project to successfully expand production!
Heavy calcium carbonate is called ground calcium carbonate, referred to as heavy calcium, which is a powder material obtained by mechanical grinding of natural carbonate minerals such as calcite, marble, limestone, dolomite, chalk, shells, etc. As a leader in the inorganic filler industry, heavy calcium carbonate is increasingly used in many fields such as plastics, papermaking, coatings, rubber, food and medicine.
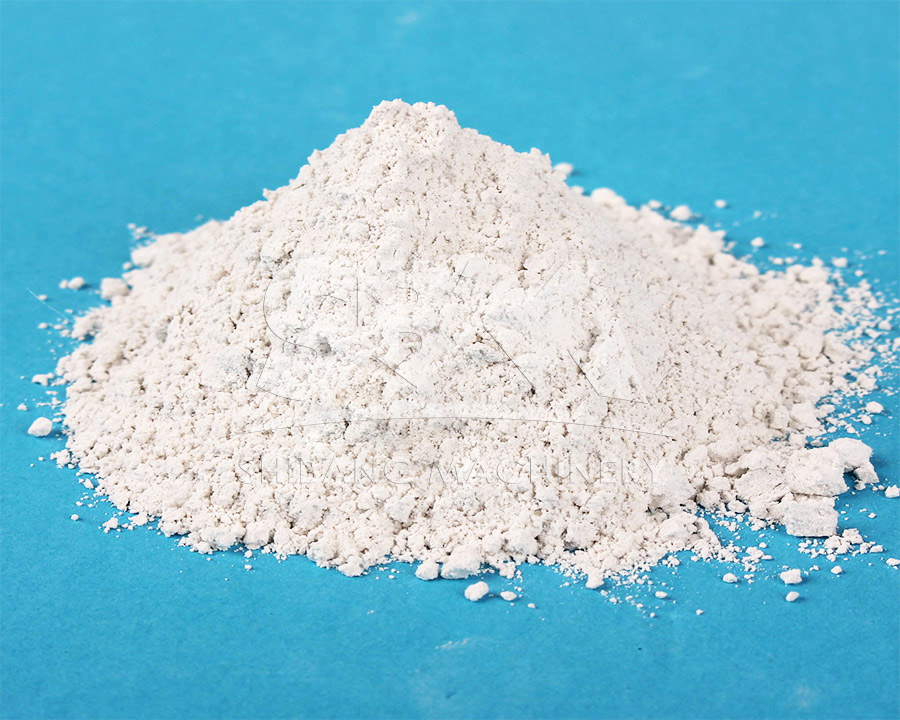
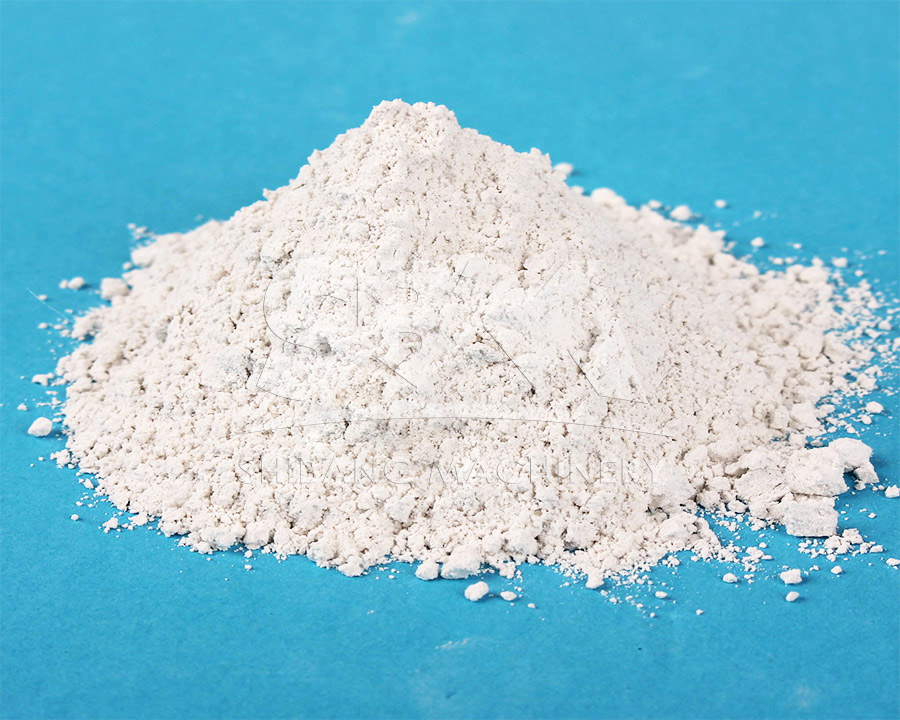
Project overview:
The user is a large domestic heavy calcium carbonate production company. Due to business expansion and production optimization needs, the company expanded the heavy calcium powder production line. Based on the good experience brought Liming Heavy Industry mill in the first phase project, in the second phase project,the user once again chose Liming Heavy Industry mill as the main equipment in the powder making process.
The entire production line of this project was planned and designed by Liming Heavy Industry, which fully combines the customer's on-site conditions. The production site is reasonably laid out and clean, helping the company to reach a new level in terms of output increase, cost control and quality assurance.
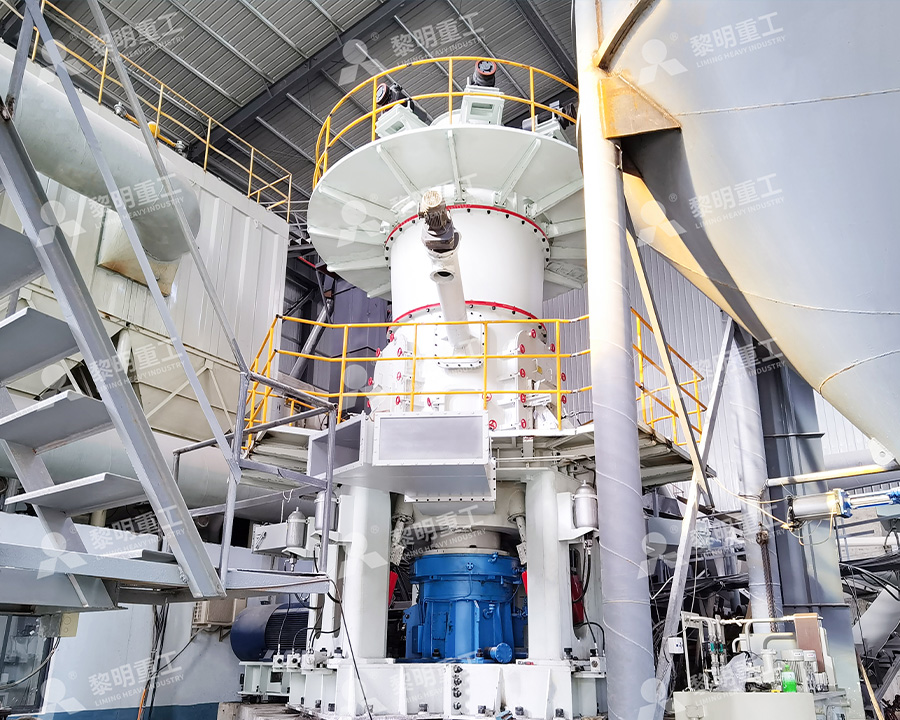
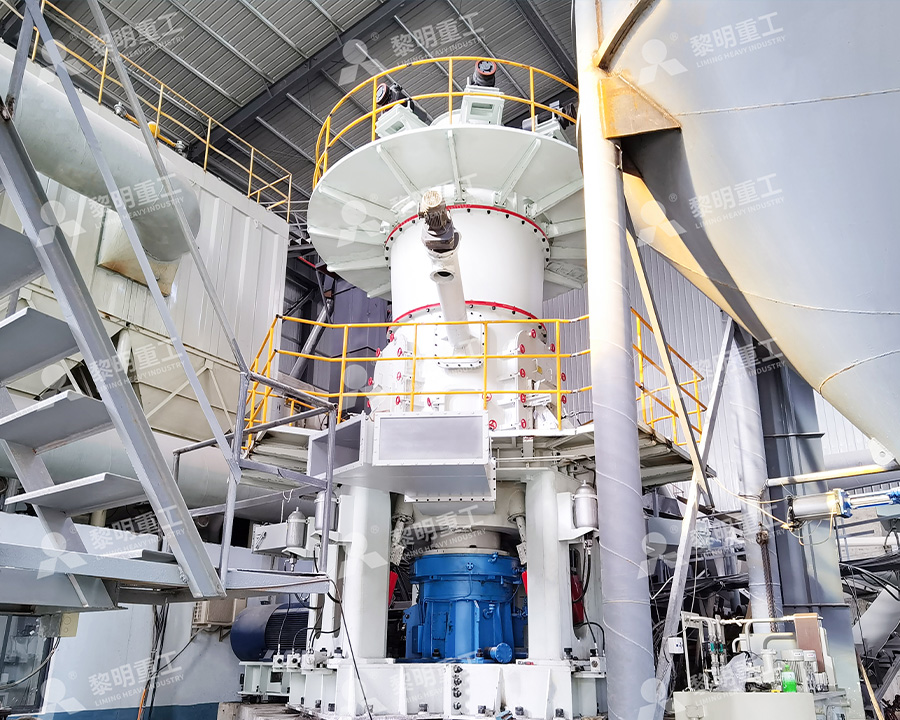
Processing materials: calcite
Equipment used: LUM ultrafine vertical mill
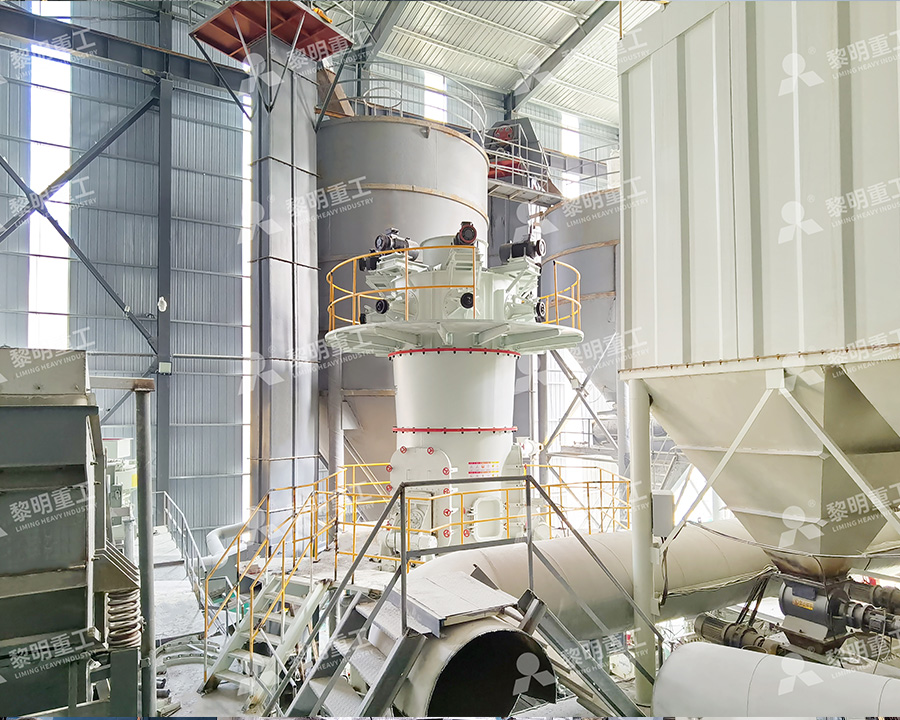
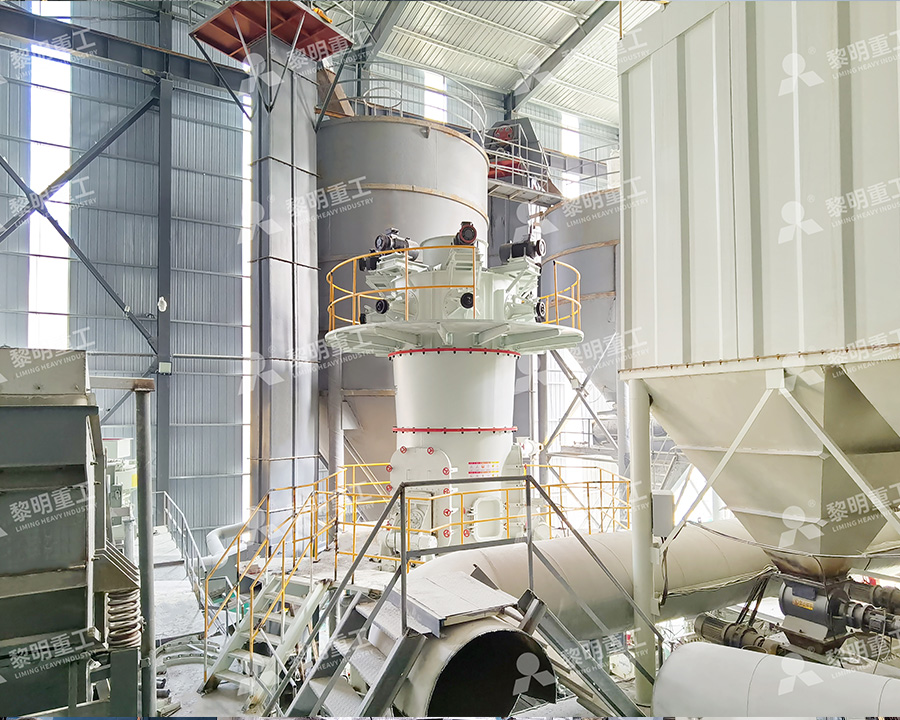
Phase I project powder production line
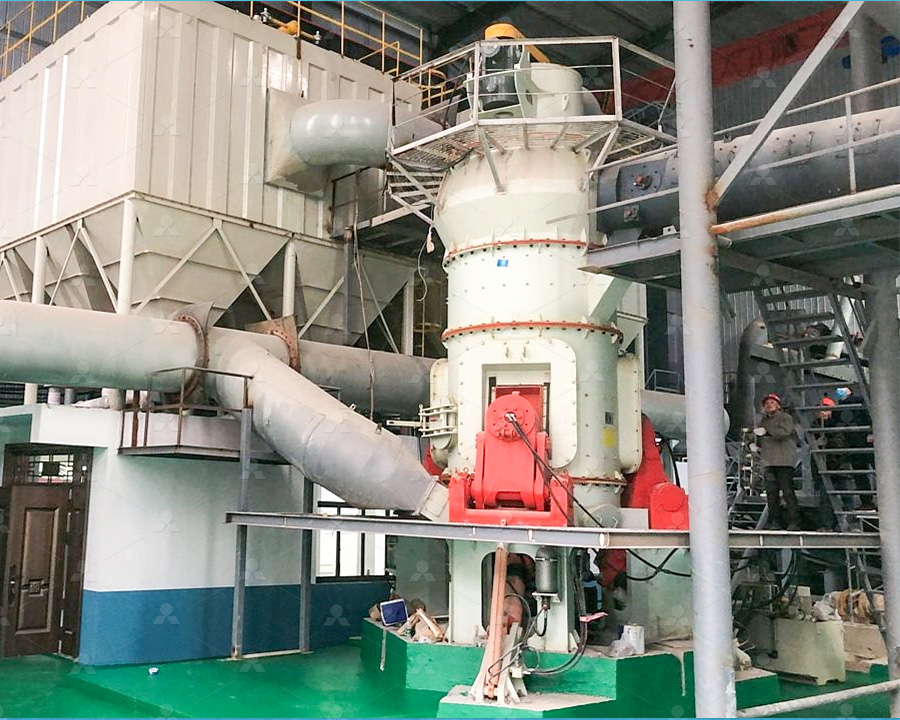
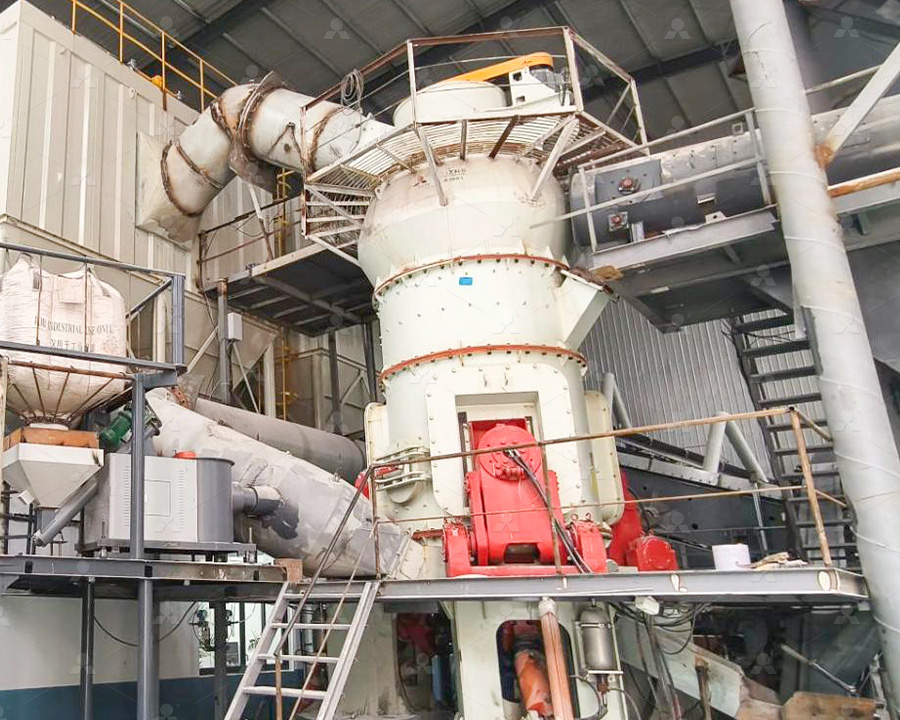
Equipment selection:

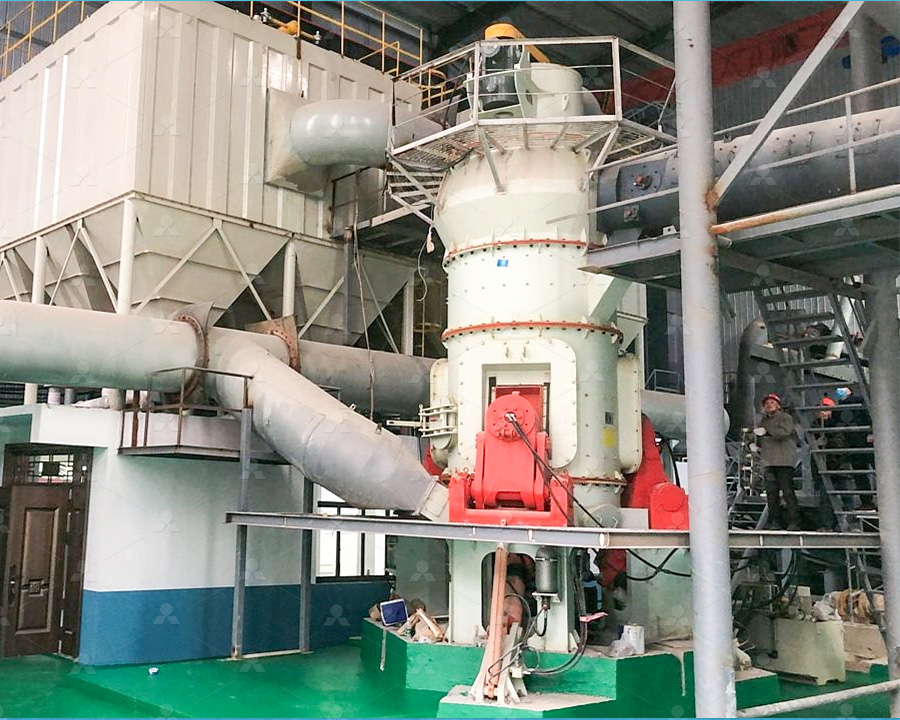
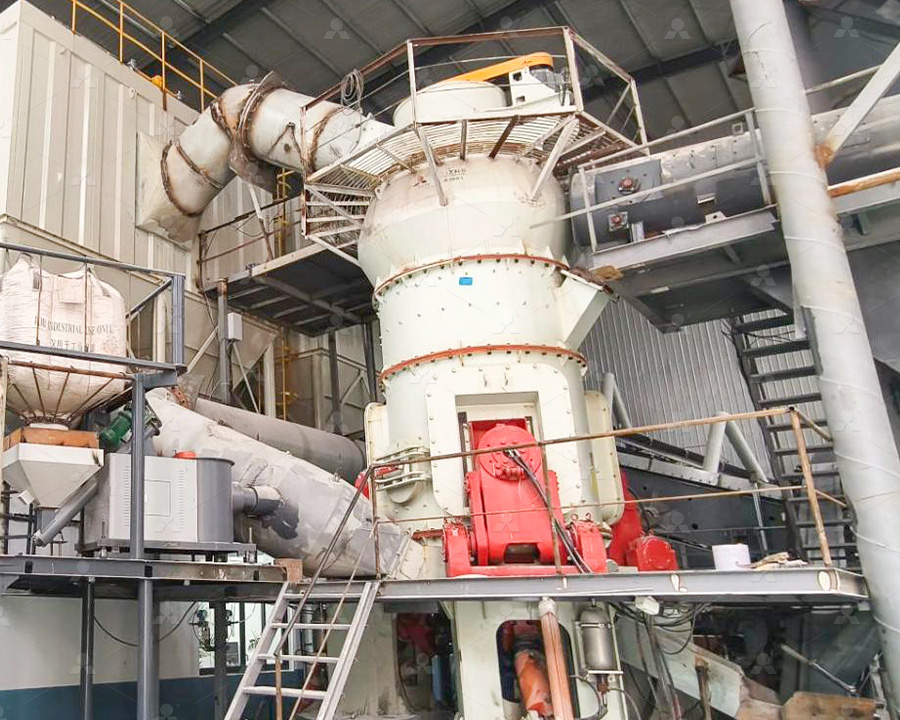
Equipment selection:

High powder selection efficiency
Using a multi-rotor powder selector, the rotors can be frequency-controlled, and the finished product fineness can be achieved within the selected range; from 45μm-3μm, a variety of qualified products can be obtained at the same time, and the 2μm content can reach more than 65%.
High whiteness of finished products
The grinding curve of the specially designed roller sleeve and liner has higher grinding efficiency and high finished product rate obtained in one grinding; at the same time, the material layer grinding principle is adopted, and the finished product has high whiteness and purity.
Intelligent roller pressure control
The roller pressure control method of PLC/DCS automatic control is adopted, and the grinding pressure control is precise, the operation is efficient and stable, and the operation is simple.
Stable operation
The electronic limit and mechanical limit protection are adopted to prevent the contact between the roller sleeve and the grinding disc liner, avoid severe vibration and destructive impact, and the operation is stable and efficient.
High degree of automation
The automatic control system is adopted, which can realize remote control, interlocking protection, reliable operation and easy operation.
Convenient maintenance and environmental protection
During maintenance, the roller can be turned out of the machine by the hydraulic device, with large maintenance space, convenient maintenance, and reduced downtime losses; the equipment is sealed as a whole, operates under negative pressure, has small vibration during operation, and no dust overflow.
Process flow:
After crushing and iron removal, the raw materials are stacked in the raw material bin through the bucket elevator. Under the condition of pre-set feeding amount, the quantitative feeder weighs the material and feeds the material into the LUM ultrafine vertical mill through the lifting and conveying equipment for grinding.
When the material enters the LUM ultrafine vertical mill, it will move evenly from the middle of the grinding disc to the edge under the action of centrifugal force. When passing through the grinding area on the grinding disc, it will be crushed by the grinding roller. Large pieces of material will be directly crushed, and fine particles will be squeezed to form a material bed for inter-particle crushing. The crushed material will continue to move to the edge of the grinding disc until it is carried away by the strong airflow at the wind ring. When the airflow passes through the upper separator, under the action of the rotor blades, the coarse particles will return to the grinding disc for grinding, and the qualified fine powder will be discharged from the mill with the airflow and collected by the system's powder collector, which is the finished ultrafine powder.
In the operation of the equipment, if there are iron blocks and other debris mixed in the processed materials, when they move to the edge of the grinding disc with the materials, they will not be blown up by the wind due to their own weight, and fall to the lower cavity of the mill and be scraped into the slag discharge port by the scraper installed at the bottom of the grinding disc and discharged out of the machine.
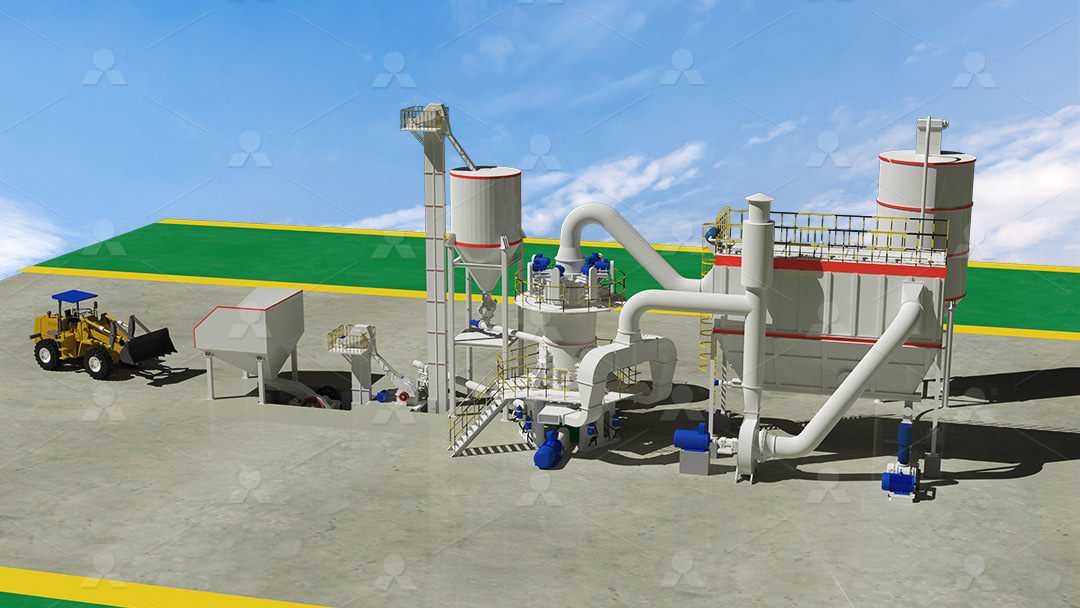
When the material enters the LUM ultrafine vertical mill, it will move evenly from the middle of the grinding disc to the edge under the action of centrifugal force. When passing through the grinding area on the grinding disc, it will be crushed by the grinding roller. Large pieces of material will be directly crushed, and fine particles will be squeezed to form a material bed for inter-particle crushing. The crushed material will continue to move to the edge of the grinding disc until it is carried away by the strong airflow at the wind ring. When the airflow passes through the upper separator, under the action of the rotor blades, the coarse particles will return to the grinding disc for grinding, and the qualified fine powder will be discharged from the mill with the airflow and collected by the system's powder collector, which is the finished ultrafine powder.
In the operation of the equipment, if there are iron blocks and other debris mixed in the processed materials, when they move to the edge of the grinding disc with the materials, they will not be blown up by the wind due to their own weight, and fall to the lower cavity of the mill and be scraped into the slag discharge port by the scraper installed at the bottom of the grinding disc and discharged out of the machine.
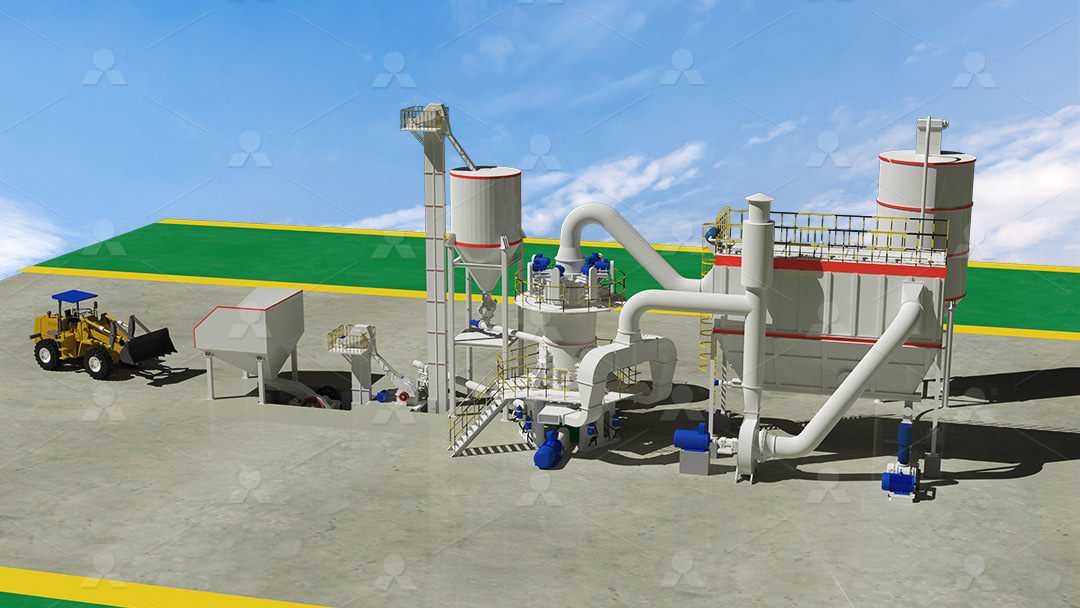